Fachbeitrag
Werkstoffkunde
19.07.25
Zirkonoxide verstehen und gezielt einsetzen
Zirkonoxid³ (Teil 2): Der Werkstoff-Faktor – Qual der Wahl oder Vielfalt ist Trumpf?
Das hochwertigste Material allein garantiert noch keine herausragenden Restaurationen. – Dieses Zirkonoxid-Paradox, das im ersten Teil der Artikelserie (dental dialogue 6/25) zur Diskussion stand, führt nun zu Teil 2, in welchem der „Werkstoff“ selbst im Fokus steht: Wie können Dentallabore durch das „Zirkonoxid-Universum“ navigieren? Und wie nutzen sie die Evolution vom opaken Gerüstmaterial zum ästhetischen Hybrid-Multilayer optimal? In der wachsenden Materialvielfalt liegen sowohl Chancen als auch Herausforderungen. Teil 2 gibt praktische Entscheidungshilfen.
Hier finden Sie Teil 1 der Reihe Zirkonoxid3
Ein gewöhnlicher Dienstag in Spenge: In der Produktionsstätte von Dental Direkt herrscht Betriebsamkeit. Die Werkstoffwissenschaftlerin Pia Wibowo nimmt eine Zirkonoxid-Ronde aus der neuen Multilayer-Presse und mustert die Oberfläche. Die hoch spezialisierte Industriepresse, aus der die Ronde stammt, ist das Herzstück der Zirkonoxid-Produktion: Die Presse verdichtet verschiedene Schichten von Zirkonoxid-Pulvern mit definierten Eigenschaften – unterschiedliche Yttriumoxid-Konzentrationen, Farb- und Transluzenzgrade – unter kontrolliertem Druck zum mehrschichtigen Rohling. Jede Mikrometereinstellung beeinflusst die Materialeigenschaften. Das Resultat sind Rohlinge mit stufenlosen Übergängen von hoher Festigkeit im zervikalen Bereich zu natürlicher Transluzenz im inzisalen Bereich. „In diesen unscheinbaren Scheiben stecken mehr als 14 Jahre Entwicklungsarbeit“, erklärt Pia Wibowo. „Als Dental Direkt mit der Produktion von Zirkonoxid begann, war es ein opakes Gerüstmaterial. Heute haben wir u. a. Hybrid-Multilayer, die unterschiedliche Yttriumoxid-Anteile in einem Rohling vereinen.“
Was vor zehn Jahren unvorstellbar schien, ist heute Alltag. Lisa Freiberg, Produktmanagerin bei Dental Direkt, bringt es auf den Punkt: „Ich liebe es, alle Trümpfe auf der Hand zu haben. Mit einer Vielzahl von Zirkonoxid-Varianten bieten wir für jede Situation die Lösung.“ (Abb. 1) Doch dies stellt Labore auch vor Herausforderungen: Welches Material passt zur jeweiligen Indikation? Was bedeuten die unterschiedlichen Generationen und Transluzenzgrade? Um Zirkonoxide besser zu verstehen, hilft ein Blick auf die Entwicklungsgeschichte.
Werkstoff-Evolution: Vom Klassiker zum Allrounder
Generationen 1 und 2: Die Klassiker (3Y-TZP)
Die ersten Zirkonoxide sind hochfeste 3Y-TZP-Materialien mit 3 Mol-% Yttriumoxid. Sie punkten mit hoher Stabilität (> 1000 MPa Biegefestigkeit) und sind opak. Generation 2 behält die 3 Mol-% Yttriumoxid bei, reduziert aber den Aluminiumoxid-Gehalt, was zu etwas höherer Transluzenz bei nahezu unveränderter Festigkeit führt. Ztm. Benjamin Mumos, Anwendungstechniker bei Dental Direkt, erklärt: „Klassische Zirkonoxide haben sich über mehr als ein Jahrzehnt im klinischen Einsatz bewährt. Für implantatprothetische Versorgungen oder zum Kaschieren verfärbter Stümpfe sind sie nach wie vor erste Wahl.“
Generation 3: Die Ästhetiker (5Y-TZP)
Mit der dritten Generation folgt ein Paradigmenwechsel: 5Y-TZP enthält 5 Mol-% Yttriumoxid, was zu etwa 50 % kubischer Phase im Gefüge führt. Das Ergebnis: eine deutlich gesteigerte Transluzenz, vergleichbar mit Lithiumdisilikatkeramik (Abb. 2 und 3). „Die kubischen Kristalle verteilen das Licht gleichmäßig in alle Richtungen und streuen es durch ihr größeres Volumen weniger an den Korngrenzen“, erläutert Christina Voß, Leiterin Forschung und Entwicklung bei Dental Direkt. Ihre Biegefestigkeit ist zwar niedriger, doch eignen sich diese Materialien sehr gut für Einzelzahnversorgungen und kleinere Brücken bis drei Glieder im Frontzahnbereich.
Generation 4: Die Hybriden (4Y-TZP und Multilayer)
Die vierte Generation repräsentiert den Status quo: 4Y-TZP bildet mit 4 Mol-% Yttriumoxid eine Balance zwischen den Eigenschaften der Generationen 2 und 3. Mit einer Biegefestigkeit um 1000 MPa bei deutlich höherer Transluzenz eignen sich diese Materialien für ein breites Indikationsspektrum (Abb. 4). „DD cube ONE ML ist ein echter Allrounder“, so Christina Voß. „Mit der hochtransluzenten Plus-Variante bietet es ausreichend Festigkeit für umfangreiche Restaurationen bei gleichzeitig natürlicher Lichtdynamik.“
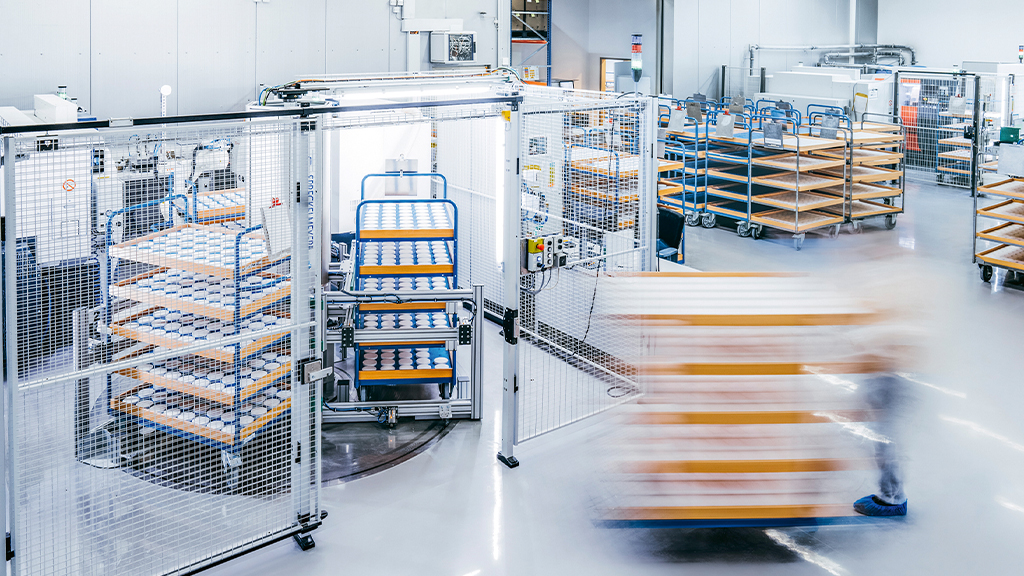
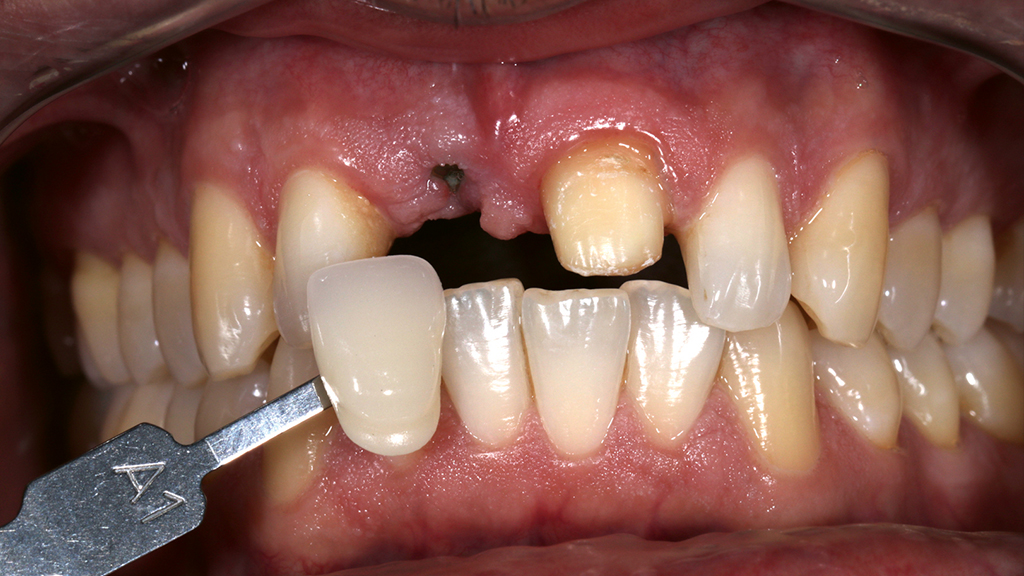
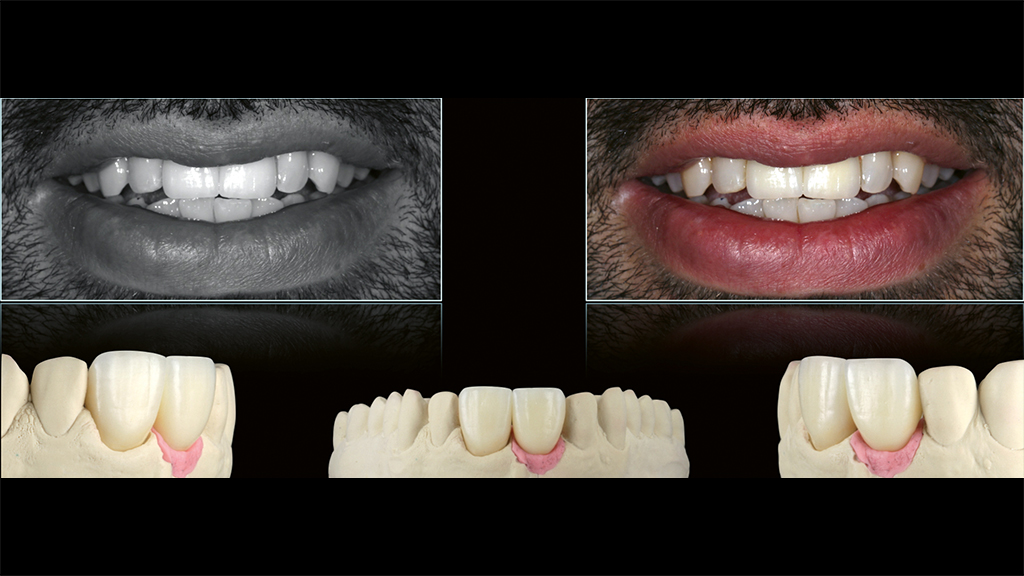
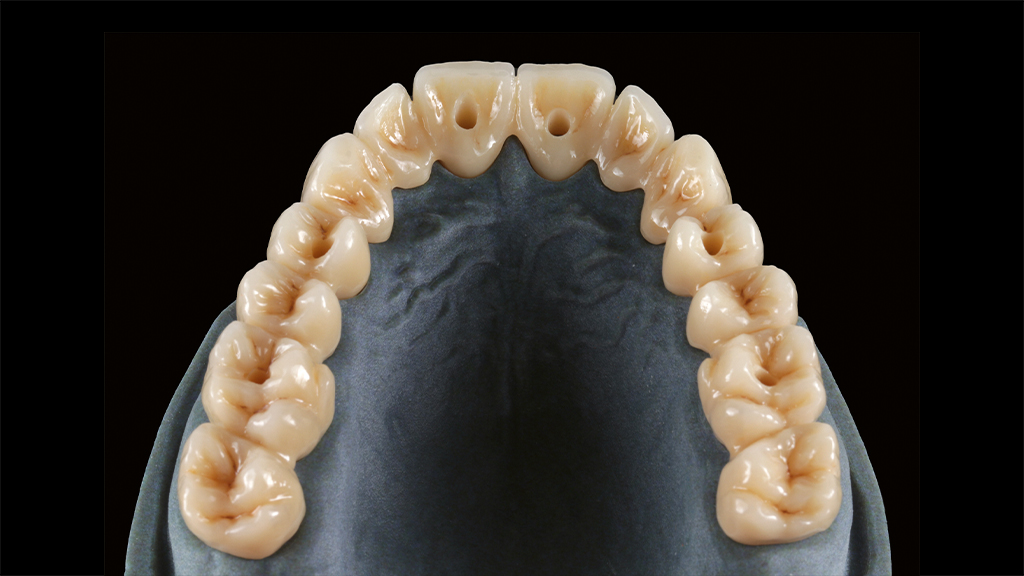
Generation 5:
Die Hybridlayer-Technologie
Neuester Entwicklungsschritt – manchmal als „5. Generation“ bezeichnet: Hybridlayer (z. B. DD cubeY HL) vereinen zwei unterschiedliche Zirkonoxid-Typen in einem Rohling. Im inzisalen Bereich sorgt 5Y-TZP für Transparenz, während im zervikalen Bereich 3Y-TZP Stabilität bietet (Abb. 5 und 6). „In die neuen ‚Y‘-Ronden sind unsere kompletten Erkenntnisse aus der Zirkonoxid-Entwicklung eingeflossen,“ erklärt Pia Wibowo. „Es ist faszinierend, wie dieses neu gedachte Zirkonoxid durch systematisches Kombinieren, Erproben und Forschen entstanden ist.“
Hersteller-Konsistenz
Die Verwendung von Zirkonoxiden eines einzigen Herstellers bietet noch mehr Vorteile als den organisatorischen Komfort: Gleiche Sinterparameter, einheitliche Farbcharakteristik, identische Schrumpfungsraten, Farbharmonie und Handling-Routinen schaffen Prozesssicherheit und reduzieren Fehlerquellen.
Jenseits der Generationen – Die Lichtdynamik
Aber die Generation allein entscheidet nicht über die Ästhetik. Ebenso wichtig ist die Lichtdynamik, die sich durch die Modifikation der Rohstoffzusammensetzung steuern lässt. Hersteller nutzen einen ausgeklügelten Rohmaterial-Cocktail: Dem Zirkonoxid-Pulver werden Additive – meist Metalloxide – in oft sehr geringen Konzentrationen beigemischt. Diese steuern die Lichtabsorption und -streuung, wodurch spezifische Farbcharakteristiken entstehen, etwa rötlich-bräunliche, rötlich-gelbliche oder gräuliche Nuancen (Abb. 7). Erst die raffinierte Kombination der Additive erlaubt es, die Lichtcharakteristik und Farbtemperatur des Zirkonoxids einzustellen. „Wir machen uns diesen nuancierten Unterschied zunutze und bieten mit zwei Ästhetik-Linien eine Möglichkeit, die Lichtcharakteristik zu steuern“, so Lisa Freiberg. Werkstoffe mit wärmerer Lichtcharakteristik erzeugen eine natürlichere Optik, während Zirkonoxide mit kühlerer Lichtdynamik klarere, brillantere Effekte ermöglichen. Andere Zirkonoxid-Hersteller haben ähnliche Ansätze entwickelt, wenngleich mit unterschiedlichen Bezeichnungen.
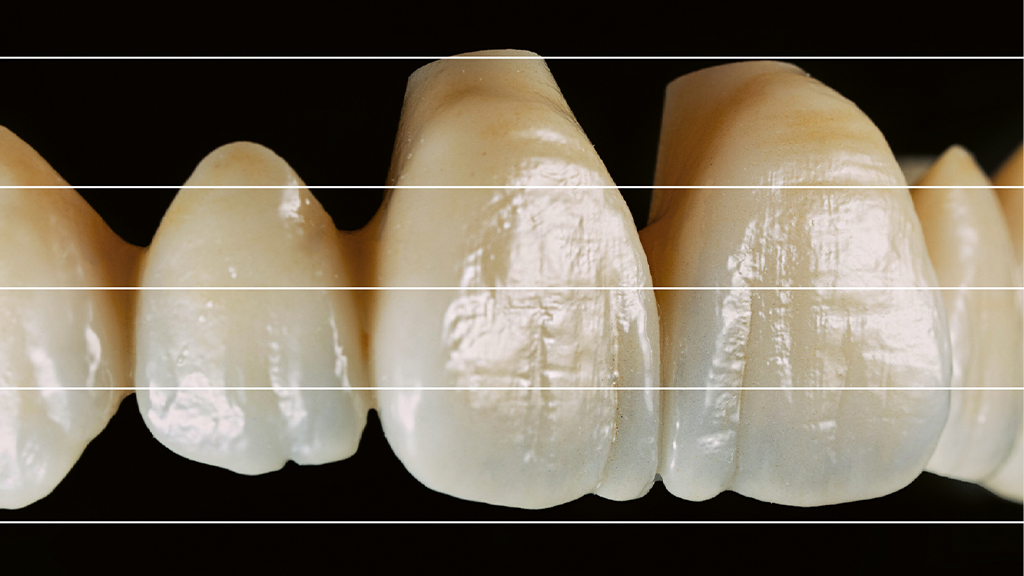
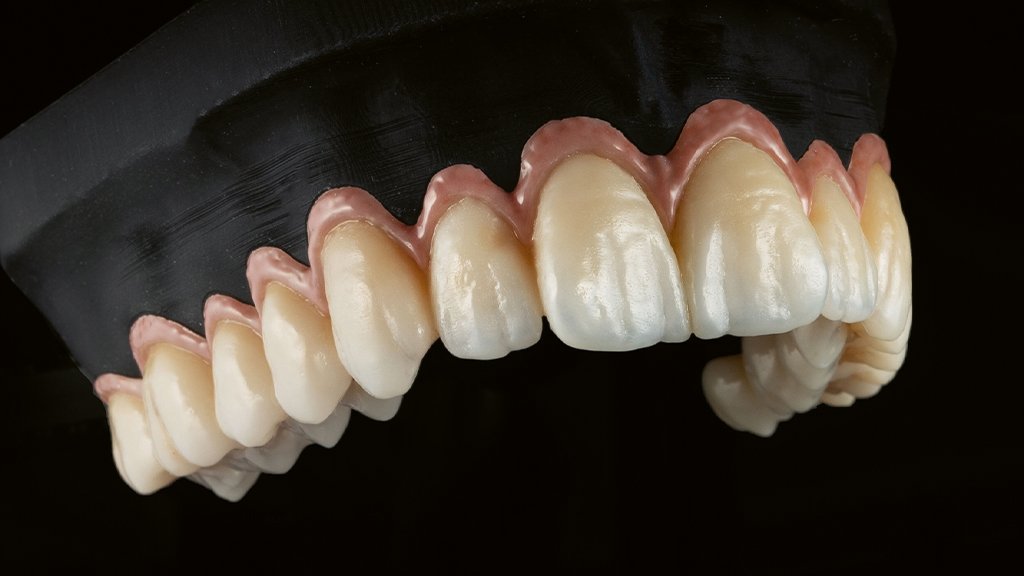
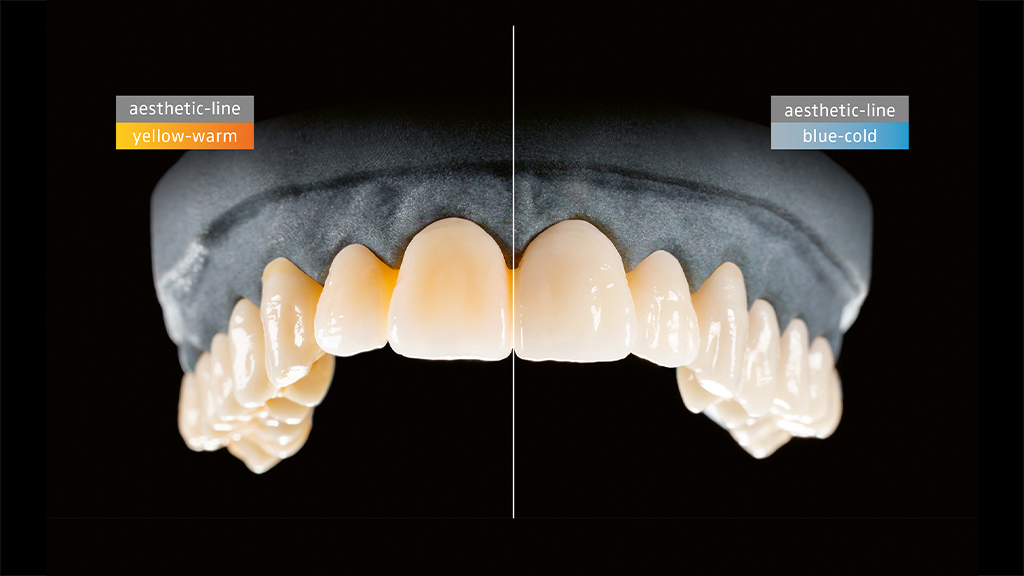
Entscheidungshilfen für die Werkstoffauswahl
Doch wie lässt sich aus dieser Vielfalt das optimale Material für den jeweiligen Fall auswählen? Im Laboralltag schleicht sich manchmal Routine ein. Man greift gern zum Bewährten, ohne für den Einzelfall die Balance aus Ästhetik, Funktion und Wirtschaftlichkeit auszuloten. Dabei liegt in der bewussten Werkstoffauswahl ein entscheidender Hebel. Es lohnt sich, grundlegende Entscheidungskriterien als Checkliste zu nutzen, z. B. Platzangebot, Anwendungsbereich, funktionelle Kriterien, Stumpffarbe, Nachbarzähne, Finalisierungsmethode.
Realitätscheck – Wann lohnt sich der Aufpreis für hochwertige Zirkonoxide?
Die Verlockung ist groß: Warum nicht das modernste Material nehmen? Das wäre einfach, aber bei Kostendifferenzen von 30 bis 50 % zwischen Standard- und High-End-Zirkonoxiden summieren sich unbedachte Materialentscheidungen schnell zu relevanten Beträgen. Der Realitätscheck zeigt: Viele Labore nutzen High-End-Multilayer dort, wo ein Standard-3Y-TZP ausreichen würde. Umgekehrt werden manchmal – oft aus Kostengründen – Standard-Materialien eingesetzt, wo die Eigenschaften der Hybridlayer den entscheidenden Unterschied machen könnten. Die „Kunst“ liegt darin, für jeden Fall das passende Material zu wählen. Denn eine durchdachte Materialhierarchie optimiert die Wirtschaftlichkeit und ermöglicht eine transparente Preisstruktur gegenüber den Zahnarztpraxen und Patienten.
Worauf bei der Herstellerwahl zu achten ist
In Zeiten, in denen günstige, oft branchenfremde Anbieter ihre Zirkonoxide am Markt platzieren möchten, lohnt sich der Blick auf die Leistungen etablierter Hersteller. Entscheidend sind nicht nur die Blankkosten, sondern die Gesamtperformance: dokumentierte Chargenkonsistenz, reproduzierbare Ergebnisse, verlässlicher technischer Support. Gerade letzter Punkt unterscheidet etablierte Anbieter oft von reinen Preisanbietern: Während günstige Alternativen meist nur das Material liefern, bieten erfahrene Hersteller umfassende Unterstützung bei Verarbeitungsfragen, Fehleranalyse und Prozessoptimierung – ein Service, der sich in der Laborarbeit als wertvoll erweist.
Nesting: Multilayer optimal nutzen
Es sind oft kleine Details, die den Unterschied machen: Beim Nesting mehrschichtiger Rohlinge kann ein einzelner Millimeter über ein brillantes oder ein mittelmäßiges Ergebnis entscheiden (Abb. 8 und 9). Björn Rose, CAD/CAM-Spezialist, bringt es auf den Punkt: „Wenn das Nesting passt, stimmt in der Regel auch die Farbe.“ Insbesondere bei Hybridlayern ist die Platzierung im Rohling entscheidend. „Wir haben systematisch Nesting-Positionen getestet und dokumentiert“, erläutert Björn Rose. „Die Ergebnisse helfen Zahntechnikern, reproduzierbare Farbresultate zu erzielen – unabhängig davon, ob sie im exocad In-CAD Nesting Modul oder in einer anderen CAM-Software arbeiten.“
Nesting-Hacks
Nutzung herstellerspezifischer Nesting-Module zur Visualisierung der Schichtgrenzen.
Bei zu hoher Positionierung (zu weit inzisal) wirken die Kronen zu hell, auch im Body-Bereich.
Die optimale Position bringt eine natürliche Aufhellung in den Höckern/der Schneide und erzeugt einen harmonischen Farbverlauf im Verhältnis zur Kronenhöhe.
Bei zu tiefer Positionierung (zu weit zervikal) fehlt die Aufhellung in den Höckern/der Schneide und das Chroma erscheint übermäßig abgedunkelt.
Sintern: Der entscheidende Schritt
1450 °C, 1580 °C oder 1500 °C? Speed oder standardisiert? Wohl nirgendwo im Prozess liegen Erfolg und Misserfolg so nah beieinander wie beim Sintern. Eine Restauration kann im Ofen ihr volles Potenzial entfalten – oder all ihre Qualitäten einbüßen. Die Palette möglicher Enttäuschungen reicht von stumpf-opaker Wirkung über grünliche Verfärbungen bis zu Passungenauigkeiten. Marianna Schmalstieg, Forschung und Entwicklung, erklärt: „Jedes Zirkonoxid benötigt eine spezifische thermische Energie. Abweichungen in der Temperatur ändern die Mikrostruktur und damit die Lichtstreuung und -durchlässigkeit.“ Auch Heiz- und Abkühlraten sowie Haltezeit beeinflussen das Ergebnis. Die Versuchung, diese Parameter zu modifizieren, ist im Laboralltag manchmal groß – sei es, um Zeit zu sparen oder Transluzenz zu steigern. Die Zirkonoxid-Spezialistin rät: „Höhere Heizraten verkürzen zwar die Sinterdauer, erhöhen aber das Risiko veränderter Materialeigenschaften.“ (Abb. 10).
Ein oft unterschätzter Faktor ist die Reinheit des Sinterofens. Verunreinigungen im Ofen werden häufig übersehen, dabei sind sie die häufigste Ursache für Verfärbungen. Grünliche Verfärbungen, milchig-weiße Areale oder dunkle Flecken – all diese Phänomene können auf Ablagerungen hindeuten, die mit regelmäßigen Reinigungsbränden zu vermeiden sind (Abb. 11a bis c).
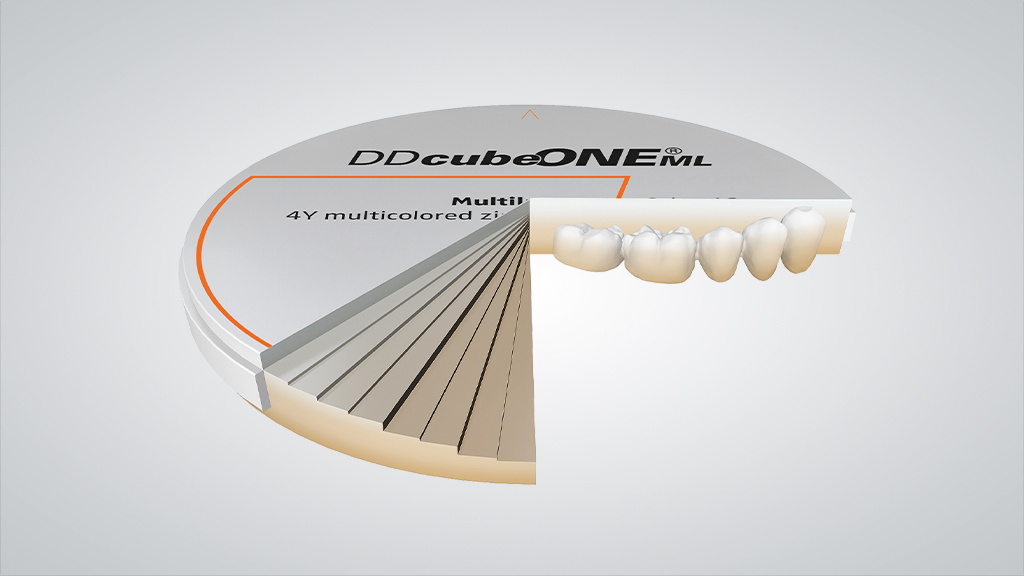
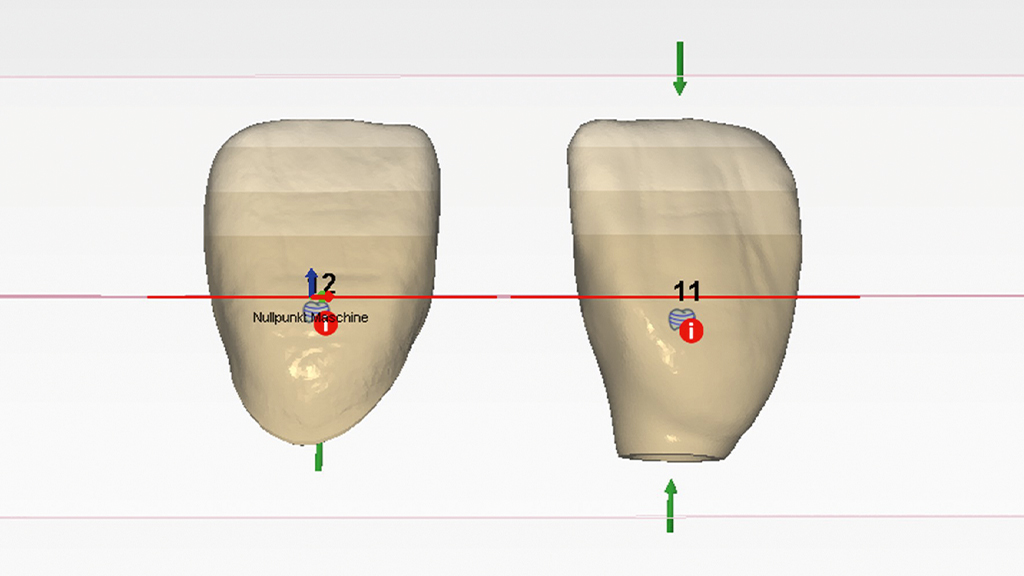
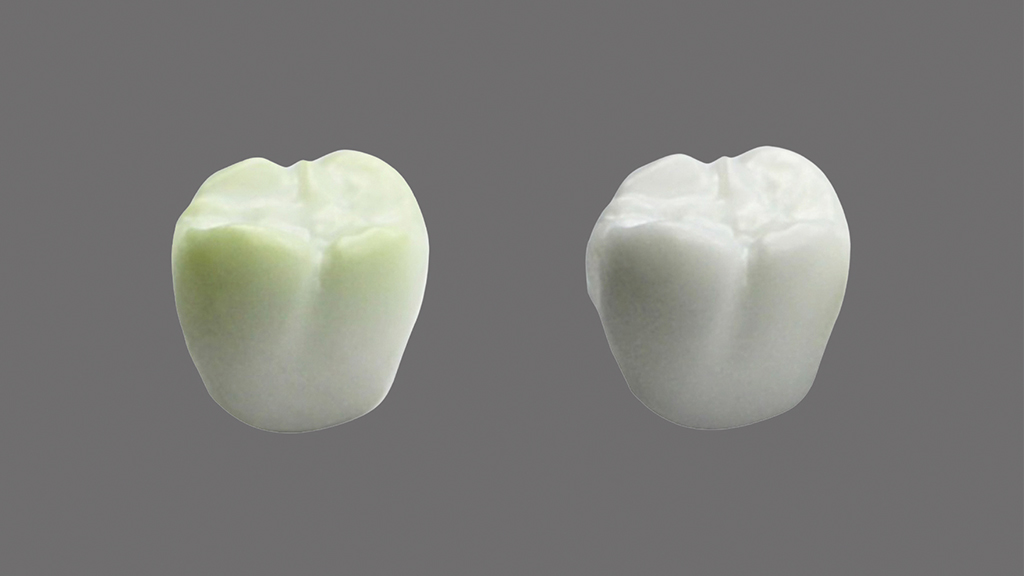
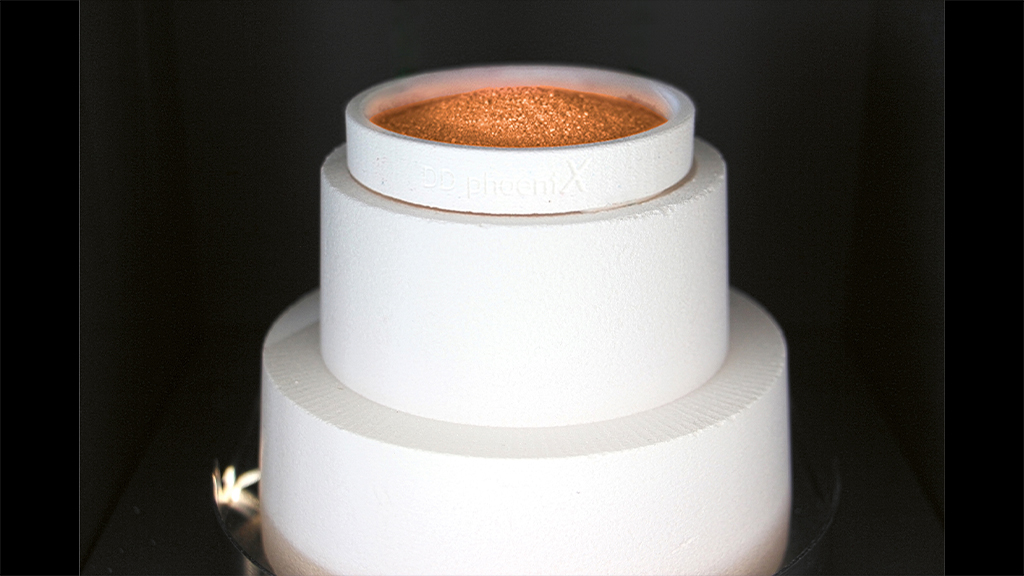
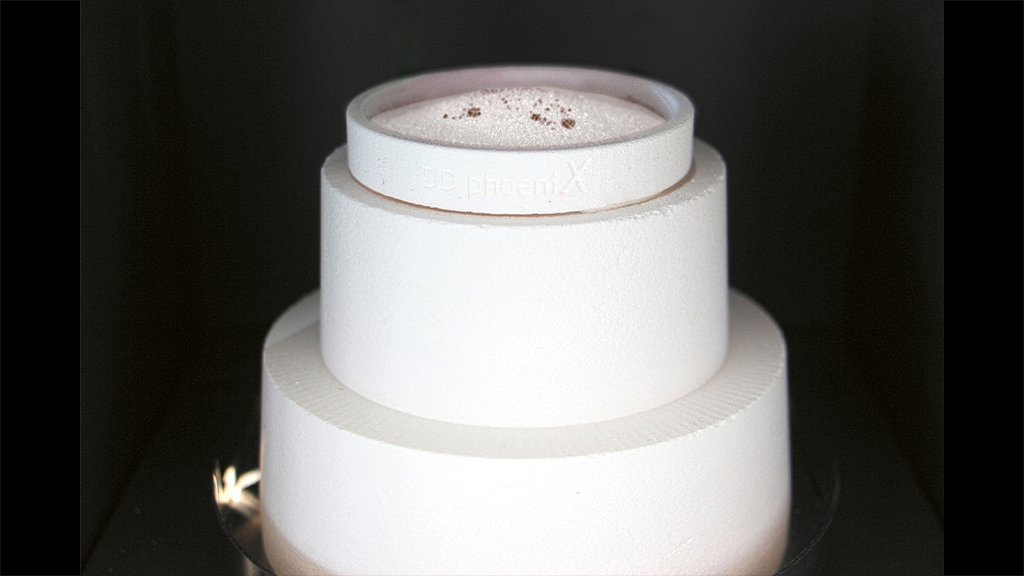
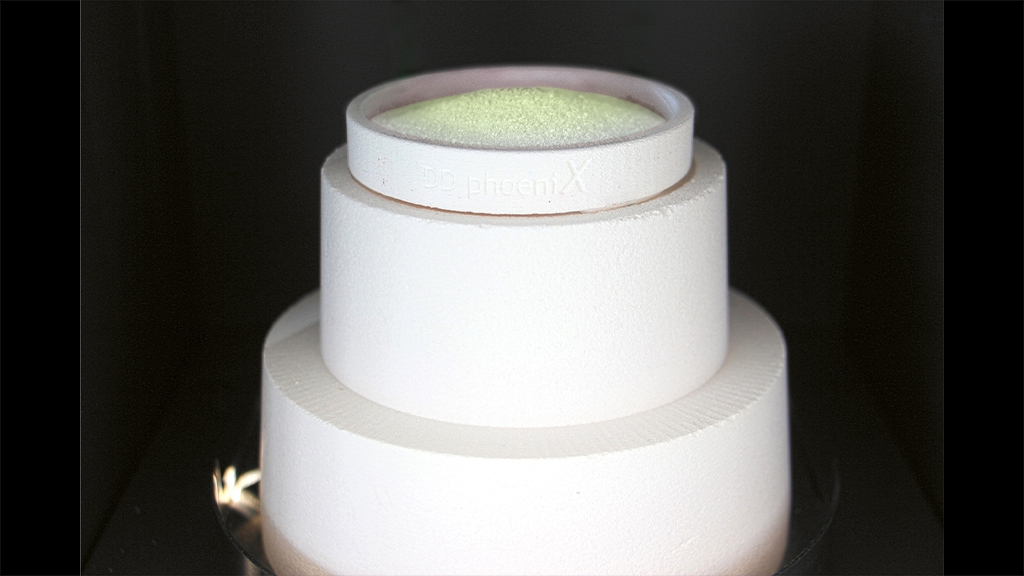
Nützliche Sinter-Hacks
- Regelmäßige Kontrolle
Heizelemente wöchentlich überprüfen: Färbungen oder weiße Beläge deuten auf Verschleiß hin
Alle zwei bis vier Wochen Reinigungsbrand (je nach Nutzungshäufigkeit) durchführen
Temperaturgenauigkeit halbjährlich mit PTC-Ringen (Process Temperature Control) prüfen - Warnsignale
Verfärbte Kontrollstücke (kleine weiße Zirkonoxid-Proben) nach dem Sintern
Milchige Flecken, grünliche oder gelbliche Verfärbungen auf Restaurationen -Verlust an Transluzenz bei eigentlich hochtransluzenten Materialien - Reinigungstipps
Sinterzubehör (Perlen, Platten, Trays) regelmäßig austauschen oder reinigen
Reinigungsbrand mit entsprechenden Reinigungsmitteln nach Herstellervorgaben
Brennkammer nur im abgekühlten Zustand und nach Trennung vom Stromnetz reinigen - Parameter-Management
Sintertabellen der Zirkonoxid-Hersteller einhalten
Speed-Sintern nur für dafür explizit freigegebene Materialien nutzen
Bei mehrgliedrigen Brücken oder hoher Ofenbefüllung längere Sinterzeiten einplanen
Sinterparameter im „Labortagebuch“ dokumentieren - Ofenbefüllung
Restaurationen nicht zu dicht nebeneinander platzieren (Mindestabstand 5 mm)
Bei hoher Befüllung Aufheiz- und Abkühlraten verlangsamen und Haltezeit verlängern
Ausblick: Der Werkzeug-Faktor als nächstes Puzzlestück
Zirkonoxid bietet heute ein beeindruckendes Spektrum an Möglichkeiten – doch selbst der beste Werkstoff entfaltet sein volles Potenzial erst bei materialgerechter Bearbeitung. Im Teil 3 der Artikelserie werden wir daher den Fokus auf den nächsten Faktor der Formel „Zirkonoxid³“ richten: das Werkzeug. Dennis Diekmann, Produktmanager bei Komet Dental, gibt einen Ausblick: „Zirkonoxid ist anspruchsvoll. Die Oberflächenbearbeitung vor und nach dem Sintern hat es in sich.“
Checkliste zur Werkstoffauswahl – Anmerkungen von Dental Direkt
DD Bio ZX² (3Y-TZP)
- Indikation: Kronen und Brücken bis 16 Glieder, Hybridabutments
- Stärken: Maximale Festigkeit (1150 MPa), hohe Opazität zum Kaschieren von Metallkomponenten oder verfärbten Stümpfen
- Anwendungen: Implantatprothetik, Gerüste für Verblendkeramik
DD cube ONE ML (4Y-TZP)
- Indikation: Kronen und Brücken bis 14 Glieder
- Stärken: Ausgewogenes Verhältnis von Festigkeit (1200 MPa) und Transluzenz, natürlicher Farbverlauf
- Anwendungen: Umfangreiche monolithische Restaurationen mit hohen ästhetischen Ansprüchen
DD cubeX² ML (5Y-TZP)
- Indikation: Inlays, Onlays, Veneers, Kronen, Brücken bis 3 Glieder
- Stärken: Maximale Transluzenz für natürliche Lichtdynamik, ähnlich Lithiumdisilikat
- Anwendungen: Frontzahnrestaurationen mit höchsten ästhetischen Anforderungen
DD cubeY HL (Hybridlayer: 3Y-TZP/5Y-TZP)
- Indikation: Kronen und Brücken bis 14 Glieder
- Stärken: Kombiniert hohe Anterior-Ästhetik mit multiindikativer Stabilität (Inzisalbereich: > 800 MPa, Bodybereich: 1050 MPa)
- Anwendungen: Umfassende Versorgungen mit abgestuften Anforderungen an Ästhetik und Stabilität
Fachbeitrag
Weitere Beiträge zum Thema