Fachbeitrag
Technik
08.02.25
HD-Milling: Jetzt kommt die Auflösung!
Möglichkeiten, von denen man im Labor bisher nur geträumt hat
Es gibt Momente im Laboralltag, in denen man denkt: „Läuft doch alles ganz gut.“ Bis plötzlich eine neue Technologie auftaucht, die vieles bisher Bekannte in den Schatten stellt. So erging es Carsten Fischer, als er zum ersten Mal mit dem CAD/CAM-Feinfräsmodus HD-Milling arbeitete. Hier erzählt er, weshalb.
Was zunächst übertrieben klingen mag, entpuppt sich als echte Veränderung für kleine und mittlere Dentallabore. Feinfräsen (HD-Milling) eröffnet Möglichkeiten, von denen man bisher vielleicht geträumt hat, die aber unerreichbar schienen: höchste Präzision bei komplexen Gerüststrukturen, minimaler Nachbearbeitungsaufwand und eine Fräsqualität, die bisher nur industriellen Fräszentren vorbehalten war.
Seit vielen Jahren arbeite ich mit CAD/CAM-Frässystemen. Angesichts der rasanten technologischen Entwicklung sehe ich nun die Notwendigkeit für den nächsten Schritt in der subtraktiven Fertigung. Der Artikel zeigt, wie ich mein Labor mit der neuen Fräsmaschine DS1 Plus von Argen mit integrierter HD-Milling-Technologie auf die nächste Stufe der CAD/CAM-Fertigung hebe. Die schlüssige Argumentation vermittelt dabei die enge Verbindung zwischen moderner Technologie und traditionellem Handwerk – fast wie eine Liebesgeschichte zwischen beiden Welten.
Quantensprung HD-Milling
„Du weißt nicht, was Dir fehlt, bis Du es einmal gehabt hast.“ Diese Worte passen gut zu den technologischen Innovationen in der Zahntechnik. Ein Blick zurück zeigt, wie viel sich in unseren Laboren verändert hat. Dinge, die wir vor 20 Jahren für unmöglich gehalten oder als technische Spielerei für Freaks abgetan haben, sind heute unverzichtbar. Und oft erkennen wir Lücken in Prozessen erst, wenn eine neue Technologie sie schließt. Als Zahntechniker, die handwerkliche Tradition und technologische Entwicklung schätzen, sind wir immer auf der Suche nach Optimierungen. Und manchmal stoßen wir dabei auf echte Quantensprünge. So erging es uns mit dem HD-Milling – einer neu gedachten CAD/CAM-Frästechnologie, die unseren Laboralltag auf das nächste Level gehoben hat (Abb. 1).
Vom Fortschritt zum Wandel
Für kleinere und mittlere Labore ist es oft eine Herausforderung, mit der rasanten Entwicklung im CAD/CAM-Bereich Schritt zu halten. Einerseits müssen wir unser Wissen ständig aktualisieren, andererseits kämpfen wir mit Fachkräftemangel und der Frage, wie sich unsere Investitionen amortisieren lassen. Seit mehr als einem Jahrzehnt arbeiten wir nun mit der CAD/CAM-Technologie. Maschinen sind präziser geworden, Werkstoffe vielseitiger, Arbeitsabläufe effizienter. Gleichzeitig sind die Ansprüche gestiegen, der wirtschaftliche Druck hat zugenommen und Therapieverfahren haben sich weiterentwickelt. Die traditionelle dentale CAD/CAM-Technik mit ihren Fortschritten in der Maschinentechnologie war zweifellos hilfreich, aber jetzt scheint es an der Zeit, neue Wege zu gehen. Hier kommt das HD-Milling ins Spiel; für uns nicht nur eine Weiterentwicklung, sondern das Fräsen 2.0. Es eröffnet uns als Dentallabor Möglichkeiten, die wir bisher nicht erreichen konnten: Präzision in komplexen Situationen, minimale Nacharbeit und eine bisher unerreichte Reproduzierbarkeit. Das HD-Milling erhöht im ersten Moment nicht die Qualität unseres finalen Zahnersatzes – die war schon immer hoch –, aber es steigert Ergebnisqualitäten und ihre Vorhersagbarkeit, Produktionssicherheit, Effizienz und Wirtschaftlichkeit. Begeben wir uns gemeinsam auf eine kleine Reise durch die Welt des CAD/CAM-Fräsens in kleinen bis mittleren Dentallaboren.
Status quo: traditionelle CAD/CAM-Fräsmaschinen
Wir alle haben in den vergangenen Jahren unsere Erfahrungen mit dem CAD/CAM-Fräsen gemacht – mal mehr, mal weniger „schmerzhaft“, aber in der Regel mit guten Ergebnissen. Zahntechniker, die Gerüste mit herkömmlichen 4–Achs- oder 5-Achs-Fräsmaschinen fräsen, kennen das Hauptproblem: Manuelle Nacharbeit ist in vielen Bereichen oft unerlässlich. Gründe können Unterschnitte, schwierige Präparationen oder zahlreiche andere Gründe sein. Keine Frage, unsere bisherigen Ergebnisse waren präzise und gut. Aber wenn wir ehrlich sind: Wie viel Zeit haben wir in die Nachbearbeitung investiert? Oft so viel, dass es kaum wirtschaftlich war. Aber anstatt ein Problem zu beklagen, sehen wir es lieber als „dornige Chance“ und suchen nach Lösungen. Wir wollen unsere Arbeit besser machen – nicht nur, weil es unser Anspruch ist, sondern weil die Entwicklungen in der Zahntechnik es verlangen. Wir haben fantastische Werkstoffe, fortschrittliche Technologien; und die künstliche Intelligenz wird unsere Arbeit weiter verändern. Traditionelle CAD/CAM-Maschinen stoßen nun an Grenzen. Was wir brauchen, sind Frästechnologien, die dem modernen Alltag gerecht werden. Die Lösung können CAD/CAM-Maschinen sein, die mit dem HD-Milling in eine neue Dimension des Fräsens vorstoßen. Die Präzision, die wir damit erreichen, liegt deutlich über dem, was bisher möglich war. Mit der DS1 Plus von Argen können wir das HD-Milling in unseren Laboralltag integrieren (Abb. 2). Neue Optionen in der Inhouse-Fertigung eröffnen ein breites Spielfeld. Doch jede neue Technologie bedeutet auch eine Lernkurve. Deshalb zunächst ein Blick auf die Grundlagen.
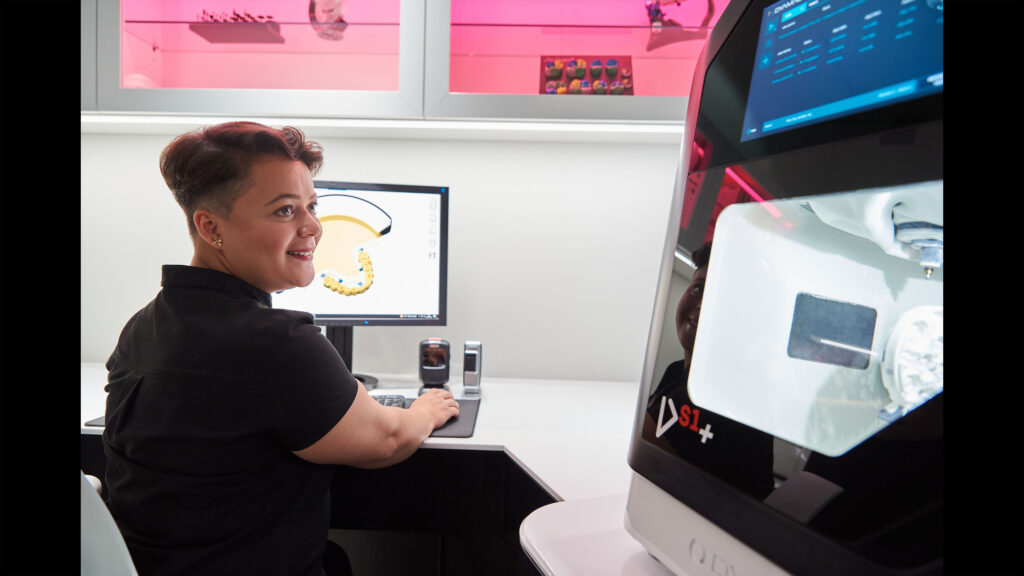
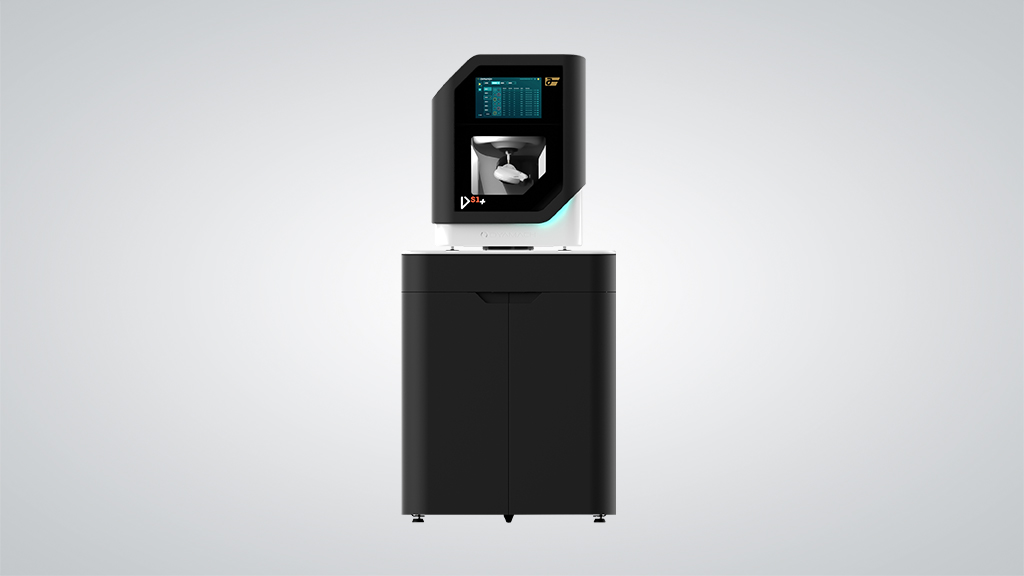
Grundlagen: Warum neue Wege gehen?
Woher kommt der Wunsch, neue Wege zu gehen? Ganz einfach: Wir wollen besser werden. Neben den Möglichkeiten, die uns eine kompakte 5-Achs-Fräsmaschine bietet, geht es uns vor allem um eines: bestmögliche Auflösung und Passgenauigkeit. Fräsmaschinen arbeiten mit einem Koordinatensystem, das aus Linearachsen (X, Y, Z) und Rotationsachsen (A, B, C) besteht. Dieses System steuert die Bewegung des Werkzeugs relativ zum Werkstück.
Linearachsen vs. Rotationsachsen
In einem Koordinatensystem steuern die Linearachsen (X, Y, Z) geradlinige Bewegungen, ähnlich wie ein Zug auf Schienen fährt. Sie bewegen das Werkzeug von links nach rechts (X), von vorne nach hinten (Y) und von oben nach unten (Z). Die Rotationsachsen (A, B, C) hingegen ermöglichen kreisförmige Bewegungen um eine feste Achse – wie bei einem Karussell, bei dem sich das Werkzeug um die jeweiligen Achsen dreht, um komplexe Winkel und Geometrien zu erreichen (Abb. 3).
Linearachsen:
- X-Achse: Verläuft parallel zum Aufspanntisch und steuert die Bewegung des Werkzeugs von links nach rechts.
- Y-Achse: Verläuft senkrecht zur X-Achse und steuert die Bewegung des Werkzeugs von vorne nach hinten.
- Z-Achse: verläuft parallel zur Werkzeugspindel und steuert die vertikale Bewegung des Werkzeugs (von oben nach unten).
Rotationsachsen:
- A-Achse: Drehung des Werkstücks um die X-Achse
- B-Achse: Drehung des Werkzeugs um die Y-Achse
- C-Achse: Drehung des Werkzeugs um die Z-Achse
3-Achsen-Maschinen arbeiten mit den Linearachsen (X, Y, Z), während 5-Achsen-Maschinen zusätzlich zwei Rotationsachsen (meist A und B) verwenden. Diese zusätzlichen Achsen ermöglichen höhere Präzision und Flexibilität bei der Bearbeitung komplexer Geometrien, da das Werkzeug aus verschiedenen Winkeln auf das Werkstück zugreifen kann.
Status Future: CAD/CAM-Fräsen 2.0
Nun kommt das HD-Milling dazu. HD-Milling steht für „High Definition“, hochauflösendes Fräsen. Die Technologie ist mehr als ein Marketingbegriff; sie ist ein Quantensprung im CAD/CAM-Fräsen mit kompakten Maschinen. HD-Milling ermöglicht es uns, auch für schwierige Herausforderungen direkt im Labor zu realisieren. Nun mag der eine oder andere denken: „Das kann meine Kompaktfräse auch.“ Aber ehrlich gesagt: weit gefehlt. Der entscheidende Punkt ist die Fräsauflösung. Man kann diese Weiterentwicklung mit dem Wechsel vom Röhrenfernseher zu HD und Ultra HD vergleichen. Der Röhrenfernseher hat ein gutes Bild gemacht. Wir haben gesehen, was wir sehen wollten. Aber dann kam HD, und plötzlich war die Bildqualität auf einem völlig neuen Niveau. Mit Ultra HD und 4K hat sich das Ganze nochmals weiterentwickelt (Abb. 4). Heute möchten wir auf gestochen scharfe Bilder nicht verzichten. Das war ein gewaltiger Sprung. Das Gleiche gilt für das HD-Milling. Die Auflösung, die wir heute erreichen, hätten wir uns noch vor wenigen Jahren im Labor nicht vorstellen können. Und wer wünscht sich heute noch ernsthaft den Röhrenfernseher zurück? Vielleicht aus Nostalgie, aber sicher nicht wegen der Bildqualität.
Mit der DS1 Plus ist HD-Milling in eine kompakte CAD/CAM-Maschine integriert, die sich ideal für kleine und mittlere Labore eignet. Und was in der Marketingsprache so charmant klingt, basiert auf einer ausgeklügelten, wenn auch etwas trockenen Maschinentechnik. Im Wesentlichen dreht sich alles um den C-Halter zur Werkstückaufnahme und das 90°-Fräsen.
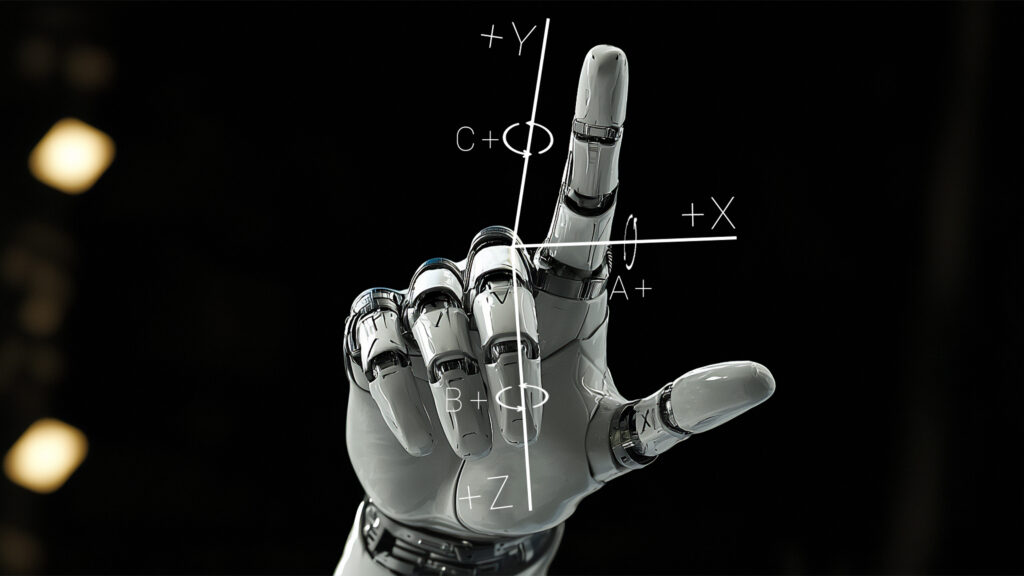
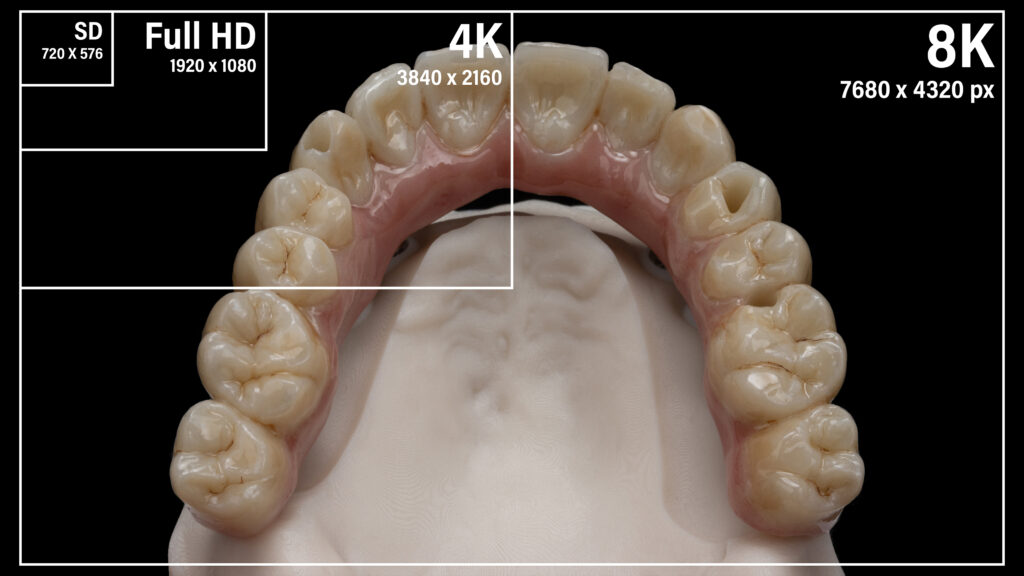
C-Halter als Dreh- und Angelpunkt
Der C-Halter ist eine Vorrichtung in CAD/CAM-Fräsmaschinen, benannt nach seiner charakteristischen C-Form. Seine Hauptaufgabe besteht darin, Fräsrohlinge sicher zu fixieren, sodass das Werkstück während des Fräsvorgangs stabil in allen Positionen bleibt. Der C-Halter ist integraler Bestandteil der 5-Achs-Kinematik in der DS1 Plus. Besonders bemerkenswert ist, dass er sich um die Z-Achse vollständig drehen kann. Diese Drehung ermöglicht es, selbst schwierigste Geometrien wie Unterschnitte und komplexe Freiformflächen in einem Arbeitsgang zu fräsen – ohne das Werkstück umspannen zu müssen. Der C-Halter ermöglicht so den Zugang zu schwer zugänglichen Bereichen des Werkstücks und sorgt für eine optimale Positionierung des Fräswerkzeuges. So können schwierige Geometrien präzise gefräst werden (Abb. 5).
Um die Ecke gedacht: 90°-Fräsen
Im Zusammenhang mit dem C-Halter steht das 90°-Fräsen. Bei dieser Form des Planfräsens stellt sich das Fräswerkzeug im 90-Grad-Winkel zur Werkstückoberfläche auf; die Schneiden stehen senkrecht zur zu bearbeitenden Fläche. Hier kommt der C-Halter ins Spiel: Er dreht das Werkstück so, dass die zu bearbeitende Fläche senkrecht zum Fräswerkzeug steht. Maschinen mit der Möglichkeit des 90°-Fräsens ermöglichen eine „stirnseitige“ Bearbeitung des Werkstücks (90°-Stellung); bislang war dies meist nur mit Industriefräsmaschinen möglich. Nun ist das 90°-Fräsen in einer kompakten Maschine, der DS1 Plus, integriert. Für uns im Laboralltag bedeutet das, dass wir jedes noch so feine Detail ansteuern können. Besonders sinnvoll ist das 90°-Fräsen für
- Unterschnitte, komplexe Innengeometrien: Präzise Bearbeitung selbst schwieriger Geometrien und Präparationen
- Hybridabutments in der Implantologie
- Brückenkonstruktionen: exakte Bearbeitung von Brückengliedern und Verbindungsstellen
- Okklusalflächen: feinste Gestaltung von Kauflächen und Fissuren
- Randbereiche: genaue Bearbeitung der Kronenränder für optimale Passgenauigkeit
- Reduzierter Druck: Reduzierter Druck auf das Werkstück, was u. a. bei dünnwandigen Bauteilen vorteilhaft ist.
Sequenzielles High-End-Fräsen
Und hier kommt das nächste Highlight: das sequenzielle High-End-Fräsen. Wir haben bei der DS1 Plus die Möglichkeit, innerhalb eines Fräszyklus verschiedene Präzisionsstufen zu definieren. Wir können entscheiden, welche Bereiche der Restauration extrem fein gefräst und welche im Standardmodus bearbeitet werden. Diese Flexibilität ist wertvoll, wenn es darum geht, Fräs- und Produktionszeiten effizient zu gestalten. Wir wollen unnötigen Zeitverlust vermeiden, gleichzeitig aber entscheidende Details perfekt herausarbeiten. Beim HD-Milling können Fräszeiten schnell in die Höhe schießen und den Workflow empfindlich stören. Daher ist das sequenzielle Fräsen für uns unverzichtbar.
Der Workflow entscheidet
Aber es reicht nicht, „nur“ eine hochmoderne Maschine zu haben. Die hochauflösende Frästechnik wird nur dann ihr Potenzial entfalten, wenn die Datenbasis stimmt (Abb. 6). Wir benötigen hochauflösende Bibliotheken, damit die Maschine die Detailgenauigkeit überhaupt umsetzen kann. Zudem muss der Workflow überdacht werden. Alle Komponenten des Prozesses müssen aufeinander abgestimmt sein.
Wir brauchen eine CAM-Software, die nicht nur eine präzise Höhenkontrolle bietet, sondern vielfältige Anpassungsmöglichkeiten, um den Fräsprozess zu steuern. Die Performance aller Bereiche – vom Scan über die Konstruktion zur CAM-Software und schließlich zum Fräsen – spielt eine entscheidende Rolle (Abb. 7 und 8). Hier zeigt sich wieder, wie wichtig ein durchdachter und valider Workflow in der Zahntechnik ist.
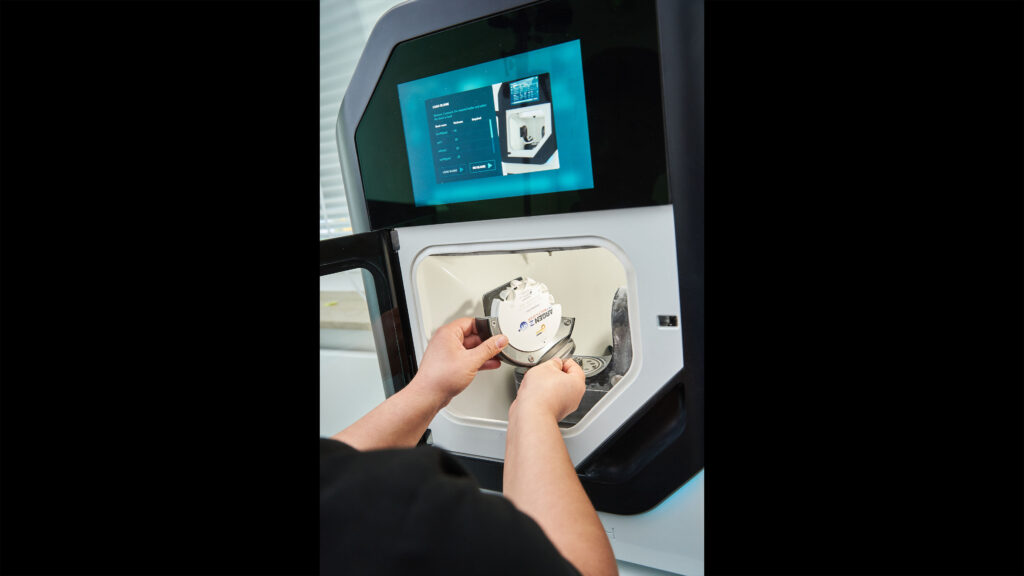
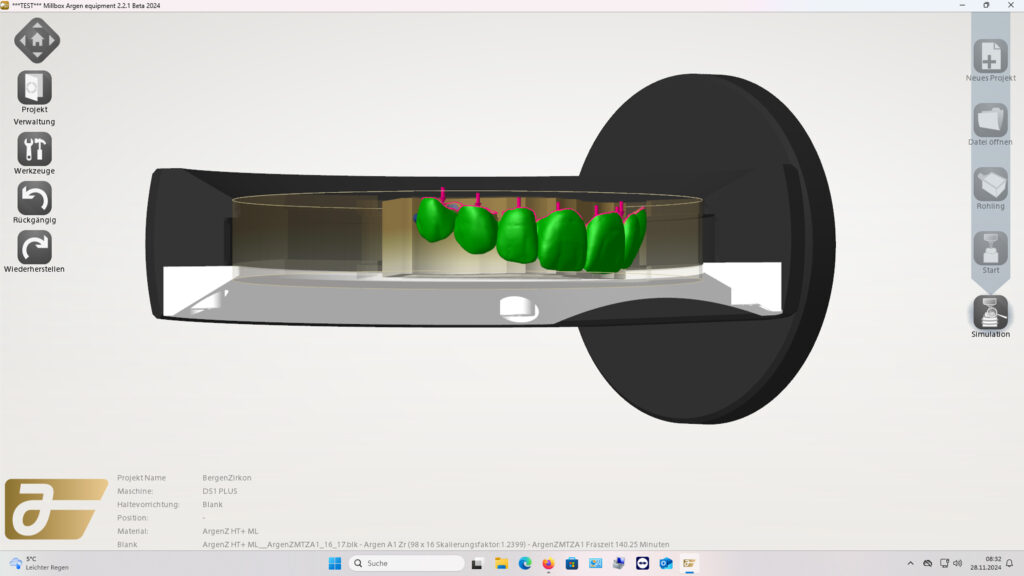
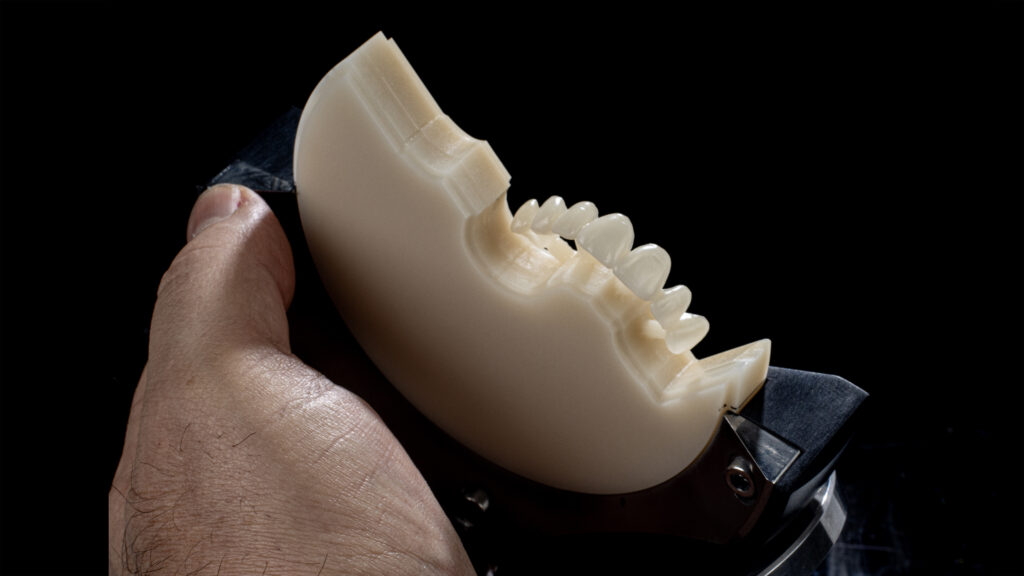
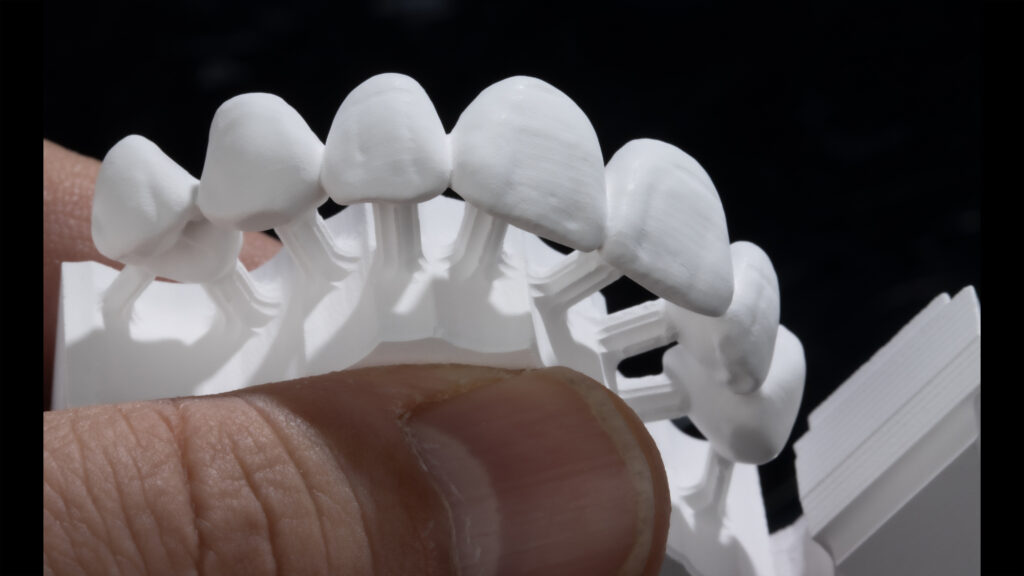
Wo steckt das HD-Milling eigentlich drin?
Wir haben nun viel über HD-Milling gesprochen, aber wo steckt diese Technologie drin? Argen geht diesen Weg mit einer Reihe von kompakten CAD/CAM-Maschinen. In Zusammenarbeit mit dem CAM-Maschinenspezialisten Dyamach vertreibt Argen die Maschinen exklusiv im deutschsprachigen Raum. Wir arbeiten mit der DS1 Plus. Diese Maschine ermöglicht sowohl Trocken- als auch Nassbearbeitung. Zudem können innerhalb eines Zyklus unterschiedliche Fräslevel definiert werden. Trotz fortschrittlicher Technologie bleibt die Maschine für uns als Anwender zugänglich. Sie ist einfach zu bedienen und lässt uns ihre Leistungsfähigkeit ausschöpfen, ohne dass wir uns in komplizierten Abläufen verlieren. Was die Arbeit zusätzlich erleichtert, ist die umfassende Unterstützung durch Argen. Bei Problemen gibt es die Möglichkeit der Fernwartung. Über TeamViewer kann das Support-Team in Echtzeit auf die Maschine zugreifen, inklusive Videokameras. Für uns bedeutet das: schnelle Hilfe ohne lange Stillstandzeiten.
Blick in den praktischen Laboralltag
In unserem Labor fräsen wir hauptsächlich Werkstoffe wie Zirkonoxid, Wachs, PMMA, PEEK, Komposit und Kunststoffe (Trockenfräsmodus). Was uns im Alltag immer wieder beeindruckt, ist die konstante Fräsqualität – unabhängig davon, ob wir mit PMMA oder Zirkonoxid arbeiten. Es kommt immer mehr auf kleinste Details an; gerade beim monolithischen Fräsen ist das entscheidend. Hier zeigt sich der wirtschaftliche Vorteil: Mit dem Argen HD-Milling eliminieren wir nahezu die gesamte Nachbearbeitung und potenzielle Fehlerquellen. Das spart nicht nur Zeit, sondern Kosten. Wenn man bedenkt, dass die Nachbearbeitung oft einer der größten Zeitfaktoren im CAD/CAM-Prozess war, wird deutlich, wie wertvoll die neue Technologie im Alltag und in einem wirtschaftlich immer anspruchsvolleren Umfeld ist. Die DS1 Plus hat sich bei uns in mehreren Anwendungsbereichen als unverzichtbar erwiesen:
- Implantatgetragene All-on-6-Versorgungen – vom Prototypen zur finalen Versorgung
- 1:1-Umsetzung komplexer Visualisierungen: monolithische High-End-Fertigung
- Monolithische Seitenzahnversorgungen: präzise Überführung in finale Werkstoffe
Patientenfall
Die Patientin erhielt sechs Implantate im zahnlosen Oberkiefer (Abb. 9 bis 18). Für die prothetische Versorgung war eine verschraubte Brücke aus Zirkonoxid vorgesehen. In solchen Fällen tragen Patienten in unserem Workflow zunächst einen Prototypen aus PMMA – ähnlich einem therapeutischen Provisorium. Dieser dient dazu, Informationen zu sammeln, die 1:1 auf die endgültige Brücke übertragen werden. So können wir frühzeitig ästhetische und funktionelle Aspekte prüfen. Anpassungen in Form, Farbe und Position der Zähne können vorgenommen, Okklusion und Funktion überprüft und optimiert werden. Obwohl der Prototyp zunächst zusätzliche Kosten verursacht, spart er langfristig Zeit und Kosten, da eine bessere Planbarkeit des Ergebnisses möglich ist. Der Schritt zur finalen Restauration war früher oft mit Ernüchterung verbunden – es bedurfte viel manueller Nacharbeit, um die gewünschte Präzision zu erreichen. Heute haben wir einen sicheren Workflow, der kaum noch Nacharbeit erfordert. Der Prozess läuft reibungslos: Die CAD-Restauration wird in der Konstruktionssoftware (z. B. exocad) entworfen, der PMMA-Blank in den C-Halter eingespannt und der Prototyp wird mit extrem hoher Präzision herausgefräst. Anschließend wird der Prototyp mit einer lichthärtenden Oberflächenglasur (Optiglaze, GC) individualisiert und für die Testphase im Mund vorbereitet. Nach der Testphase erfolgt die 1:1-Übertragung in Zirkonoxid (Argen HT+ML) und die finale Veredelung im Argen matchmaker Micro-Layering (GC Initial IQ One Sqin).
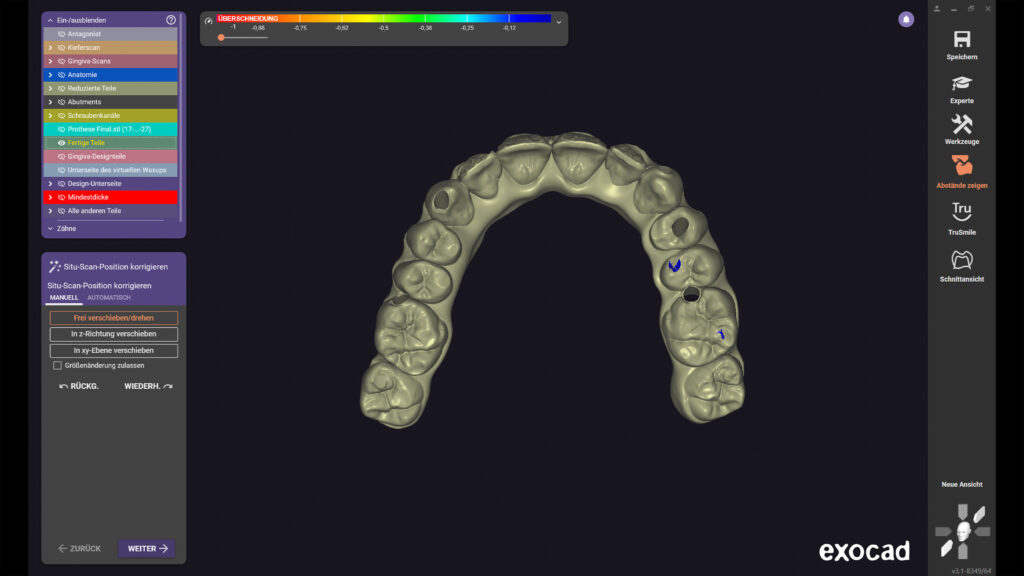

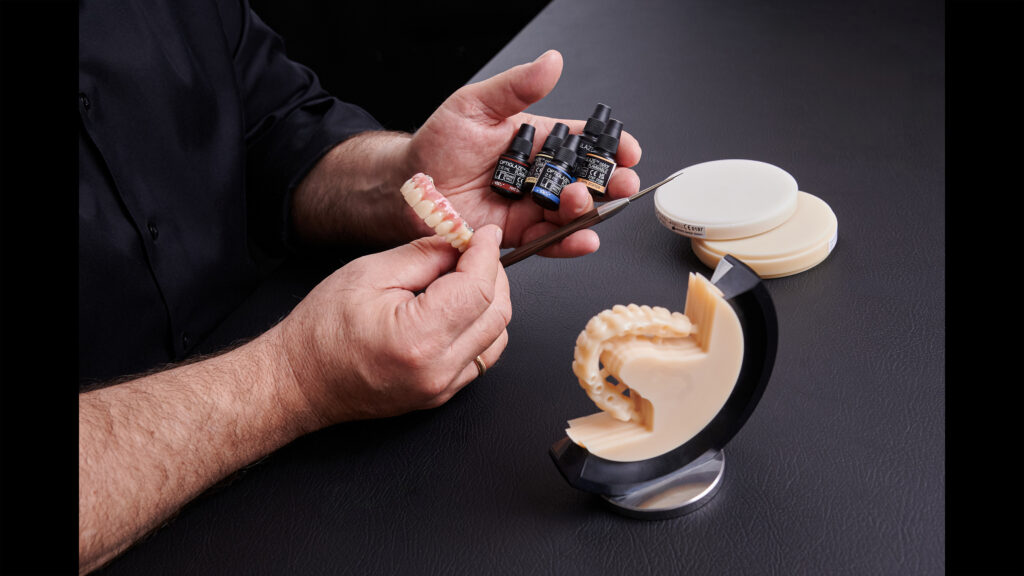
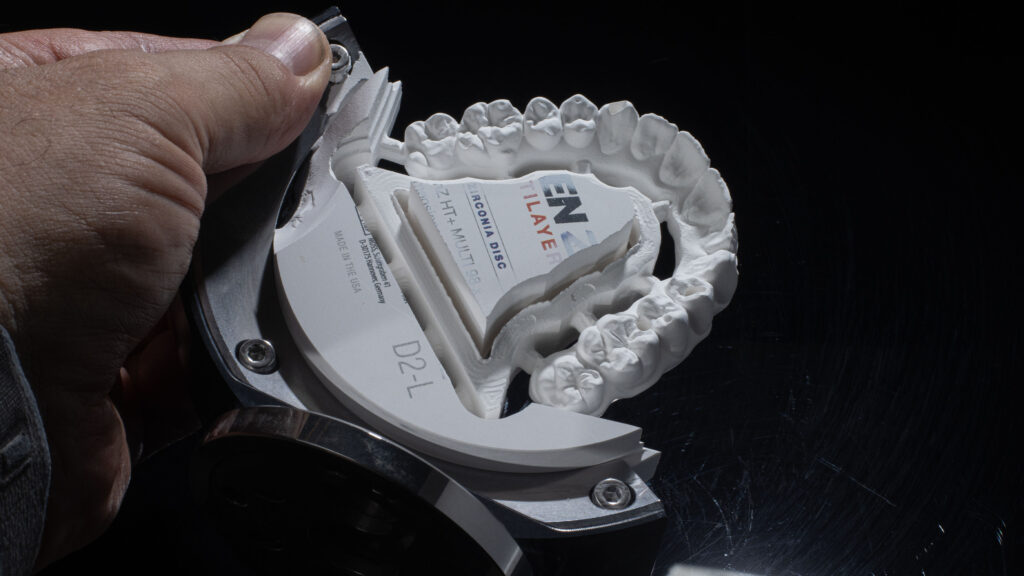
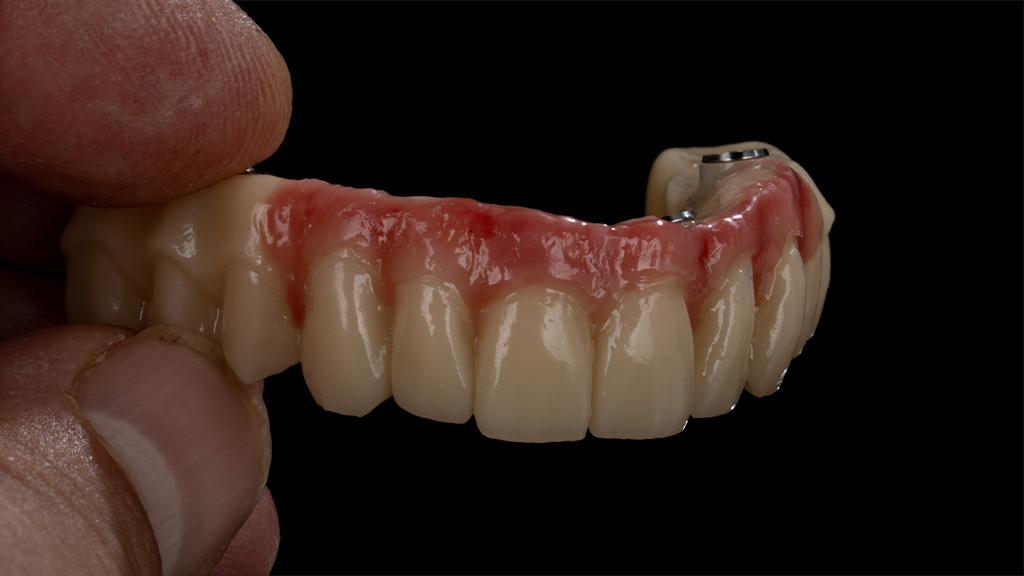
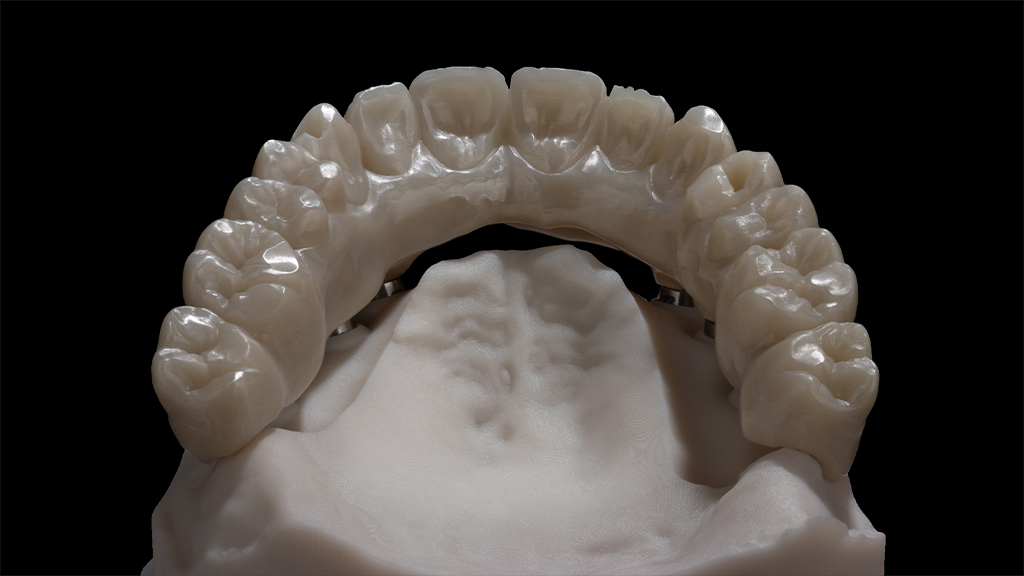
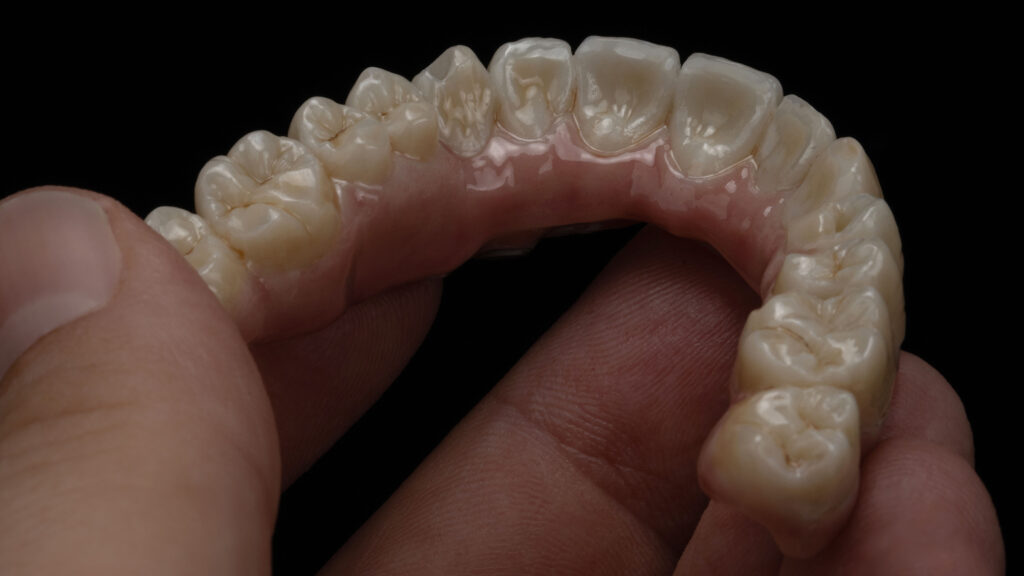
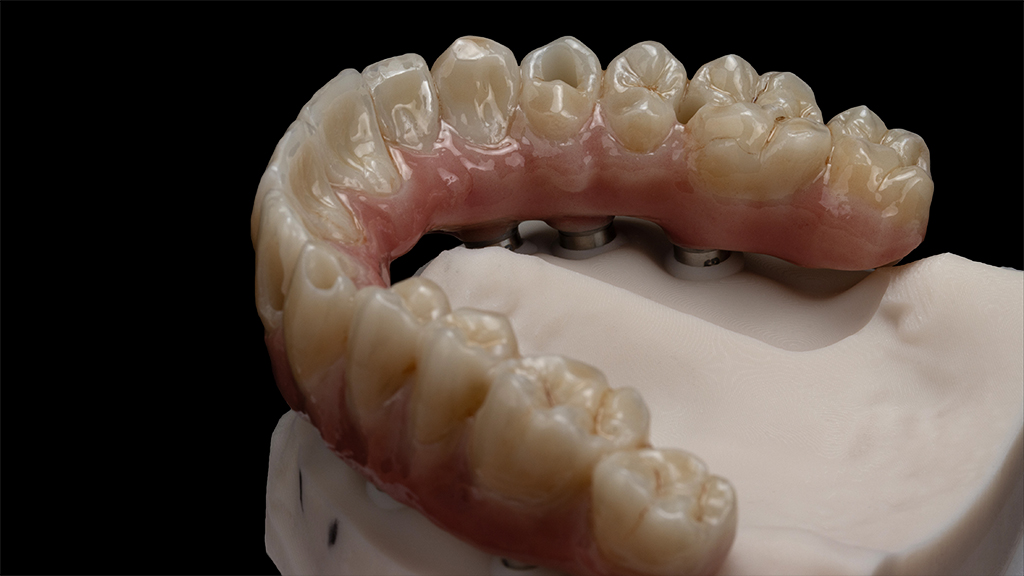
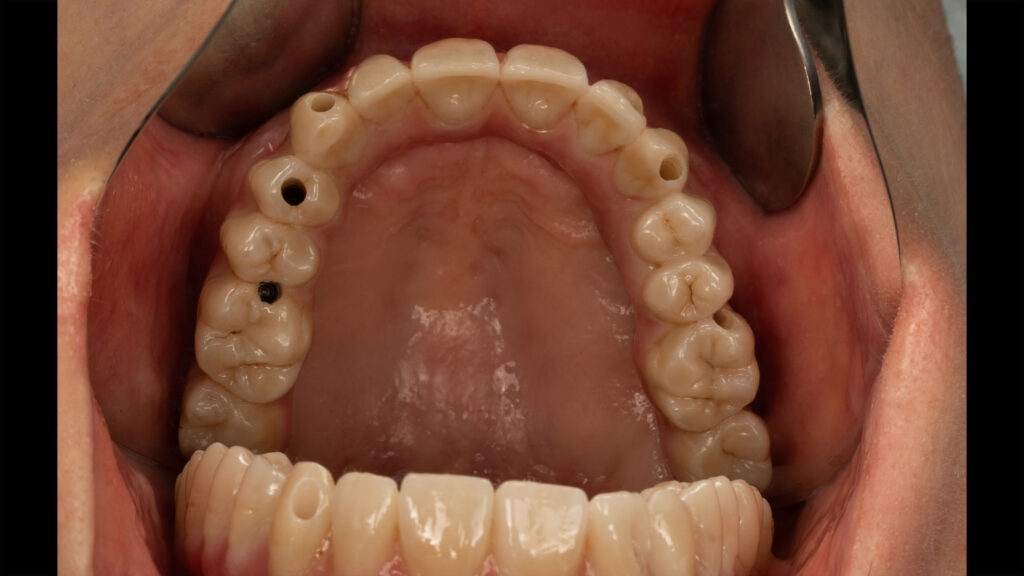
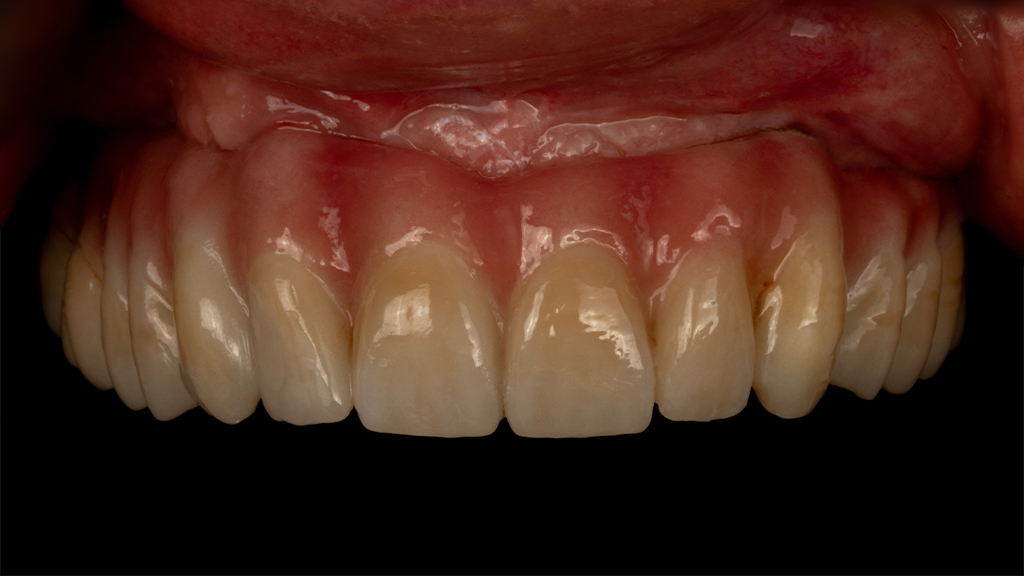
Abb. 09-18 - Die Bilder zeigen die Prozessabfolge mit HD-Milling eines Patientenfalls im Labor von Carsten Fischer: Die Patientin erhielt sechs Implantate im zahnlosen Oberkiefer. Bei umfangreichen und weitspannigen Versorgungen demonstriert HD-Milling seine Stärken, indem es durch seine Prozesssicherheit einen erheblichen Vorteil für den Betrieb bietet.
Fazit: Neue Dimension der Auflösung
„Du weißt nicht, was Dir fehlt, bist Du es einmal gehabt hast.“ So ist es mit HD-Milling. Was zunächst wie ein weiteres technisches Upgrade erschien, hat sich bei uns als Gamechanger erwiesen. Die Präzision und Effizienz, die wir mit dem HD-Milling erzielen, haben uns gezeigt, welche Lücke diese Technologie tatsächlich schließt. Von der flexiblen Materialbearbeitung bis hin zur nahezu fehlerfreien Fräsung – wir haben eine neue Dimension erreicht, die unseren Laboralltag einfacher und produktiver macht.
Oft sind es genau die Innovationen, von denen man nicht ahnt, dass man sie braucht, bis sie zeigen, wie viel mehr möglich ist – und man erkennt, dass ein Zurück schlichtweg keine Option mehr ist. Ich bedanke mich bei meinem Team, besonders bei Naomi Sulzmann sowie der Praxis Yours Smile, Dr. Rafaela Jenatschke sowie PD Dr. Peter Gehrke.
Keyfacts zum HD-Milling mit der DS1 Plus
Höhere Auflösung durch HD-Milling
- Extrem hohe Fräsauflösung
- Detailliertere und präzisere Ergebnisse
- Weniger Abweichungen
- Minimale Nacharbeit
- Höhere Genauigkeit
Herausforderungen
- Größere Datenmengen
- Höherer Rechenaufwand/Rechenleistung
- Ggf. längere Fräszyklen
Voraussetzungen
- C-Halter: Rotation des Fräsobjekts um die 4. Achse. Ermöglicht komplexe Fräsungen in hoher Qualität.
- CAM-Software: Adaptive CAM-Software, die diese Optionen unterstützt. Hochauflösende Datenbibliotheken.
- CAM-Software Argen MillBox
Vita
Carsten Fischer ist einer der bekanntesten Vollkeramik-Spezialisten Deutschlands und arbeitet seit über zwanzig Jahren mit digitalen Fertigungsprozessen. Fischer hat sich als kreativer Vordenker der Zahntechnik einen Namen gemacht. Er erkennt frühzeitig, wie sich der Markt entwickelt, und zeigt immer wieder, dass er neue Verfahren mit Weitblick bewertet und, wenn sinnvoll, in seinen Arbeitsalltag integriert. Mit seinem pragmatischen, sachlichen Ansatz sucht er stets nach Lösungen, die den Laboralltag vereinfachen und gleichzeitig reproduzierbare, hochwertige Ergebnisse liefern.
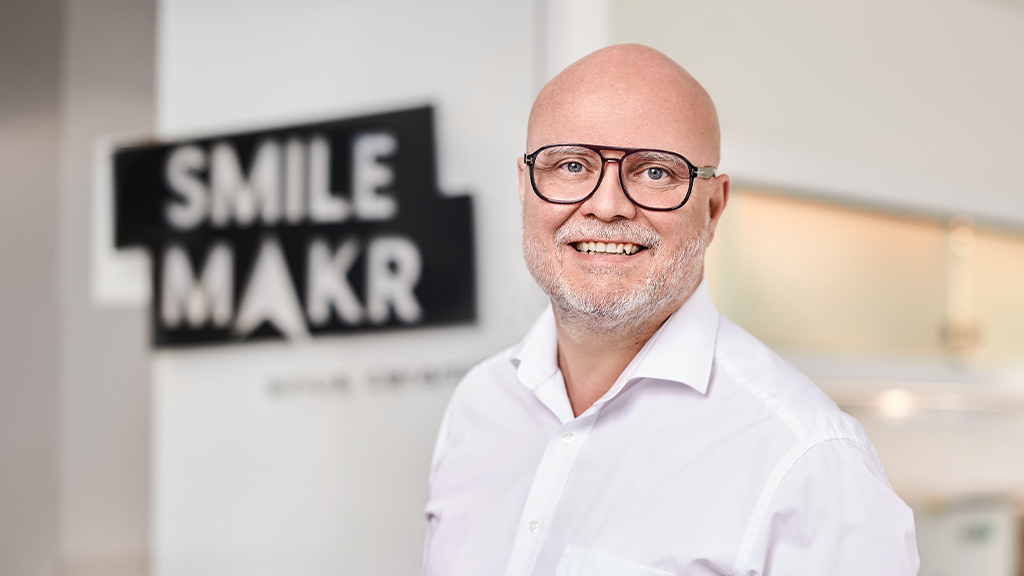
Kontakt
Sirius Ceramics | Carsten Fischer
Lyoner Strasse 44–48
60528 Frankfurt
info@sirius-ceramics.com
www.smilemakr.de
www.sirius-ceramics.com/shop/
Fachbeitrag
Weitere Beiträge zum Thema