Interview
Digitales Labor
29.05.24
Im neuen digitalen Ökosystem
Mehrwert für Kunden und Patienten im CAD/CAM-Prozess
Die Wurzeln des Dentalspezialisten Bego liegen in traditionellen zahnmedizinischen Materialien wie beispielsweise den Edelmetall- und edelmetallfreien Legierungen, Einbettmassen und Dubliermaterialien. Erfolgreich im Modellgussbereich ist Bego unter anderem mit den marktführenden Kobalt-Chrom-Legierungen Wironit sowie Wironium. Seit dreißig Jahren behauptet sich das Unternehmen aber auch mit immer neuen CAD/CAM-Technologien und -Materialien an der Spitze des Marktes. Unter anderem gelang es, mit der Selective-Laser-Melting-Technologie (SLM) die Verarbeitung von Metalllegierungen zu industrialisieren. CTO Thomas Humez beleuchtet, wie Bego digitale Lösungen und Prozesse für Zahntechniker, Zahnärzte und Patienten konsequent weiterentwickelt.
Herr Humez, Bego hat schon früh den Weg in die Digitalisierung gewagt – was war hierfür der Ansporn?
Thomas Humez: Durch die kontinuierliche Weiterentwicklung moderner Metalllegierungen und der Geräte zu deren Verarbeitung haben wir uns an der Spitze dieser Technologie gehalten. Anfang der 1990er-Jahre erkannten wir das Potenzial der aufkommenden CAD/CAM-Digitaltechnologien für die Zahnmedizin. Die Entwicklung von SLM für die CAD-gestützte Produktion von Kronen- und Brückengerüsten war revolutionär für unsere Branche. Bego war das erste Unternehmen weltweit, das den SLM-Prozess kommerziell einsetzte und hält zahlreiche Patente im Zusammenhang mit dieser Technologie im zahntechnischen Sektor. Darauf sind wir sehr stolz.
Seitdem haben wir unsere digitalen Lösungen konsequent erweitert, unter anderem durch die Einführung automatisierter CAD/CAM-Bearbeitung für Titan und Keramik. Besonders im Bereich des 3D-Drucks haben wir uns auf die Entwicklung von Spitzentechnologien für zahnmedizinische Anwendungen konzentriert. Ein Beispiel dafür ist Wironium RP, ein Metallpulver für die additive Herstellung herausnehmbarer Teilprothetik. Ein weiteres Highlight und eine Revolution für die Zahnbranche ist unser Varseo Smile Crown plus, das weltweit erste Material für den 3D-Druck von dauerhaften Restaurationen. Dieses keramikgefüllte Hybridmaterial ermöglicht eine ästhetische, schnelle und kosteneffiziente Patientenversorgung.
Auch unsere Produktion von Zahnimplantat-Lösungen wird von digitaler Technologie angetrieben. In unserem modernen Implantatproduktionszentrum werden Oberflächenbehandlungen, Endreinigung, videomikroskopische Untersuchung und Verpackung in einem hochautomatisierten Prozess unter Reinraumbedingungen durchgeführt. Unsere Kunden profitieren nicht nur von der Qualität unserer in Deutschland gefertigten implantologischen und prothetischen Lösungen, sondern auch von unseren digitalen Dienstleistungen wie technischer Support, chirurgische Planung und CAD-Design.
Was waren die größten Herausforderungen in der Entwicklung des digitalen Prozesses für Teilprothetik?
Humez: Von Beginn an hatten wir das Ziel, unseren Kunden innerhalb zweier Tage die bestmögliche Qualität zu liefern. Unsere digitale Prothetik muss eine perfekte Formtreue und eine hochglänzende Politur aufweisen. Das Material sollte eine hohe Duktilität bieten, damit die Klammern der Teilprothetik sich mehrmals „aktivieren“ lassen.
Die erste große Herausforderung war, ein biokompatibles Metallpulver für diese Anforderungen zu entwickeln. Daraus entstand unser Wironium RP Metallpulver.
Die digitale Herstellung von Teilprothetik umfasst diverse Prozessschritte: angefangen von der Datenaufbereitung über den SLM-Prozess selbst, thermische Behandlungen, Strahlvorgänge bis hin zu manuellen und automatisierten Bearbeitungen. Diese Schritte interagieren stark miteinander und wir mussten die Parameter so definieren, dass sie den Anforderungen gerecht werden.
Unsere Parameter mussten außerdem eine große Vielfalt an Geometrien – wie Anzahl und Typ der Klammern, Klammerauflagen, Gestaltung des Sublingualbügels oder der transversalen Verbindungen, Retentionsfelder, Wanddicken usw. – ohne Qualitätsverlust abdecken können. Um die Prozessgrenzwerte zu definieren, wurden umfangreiche Tests durchgeführt. So entstanden unsere Designvorgaben für Teilprothetik, die eine hohe Qualität sicherstellen.
Nicht zuletzt müssen auch Produktionsmaschinen und -technologien unsere Anforderungen hinsichtlich Prozessstabilität, -flexibilität und -effizienz erfüllen. Dies erreichten wir mit intensiven Benchmark-Studien mit verschiedenen Technologien und Maschinen.
Inwieweit vereinfacht diese Entwicklung Arbeitsprozesse?
Humez: Heute decken digitale Lösungen einen wesentlichen Teil des zahnmedizinischen Arbeitsablaufs ab und werden dies in Zukunft noch weitergehend tun. Wir befinden uns derzeit in einem vollkommen neuen Ökosystem.
Die Digitalisierung ermöglicht es, zeitaufwendige und kostspielige Prozessschritte zu vereinfachen oder vollständig zu eliminieren. Im Bereich der Teilprothetik entfallen manuelle und fehleranfällige Arbeitsschritte wie das Anstiften, Einbetten und Gießen gänzlich. Bei Bedarf können Teilprothesen problemlos reproduziert werden. Digitale Prozesse lassen sich besser automatisieren, was wiederum schnell und kostengünstig zu hochwertigen, reproduzierbaren und zuverlässigen zahnmedizinischen Restaurationen führt.
Die Digitalisierung kann außerdem dem zunehmenden Mangel an Fachkräften entgegenwirken. Dies gilt insbesondere für die Herstellung von Teilprothetik, deren analoge Fertigung spezielle Kenntnisse erfordert, die zunehmend schwerer zu finden sind. Die Digitalisierung macht Arbeitsplätze für die neue Generation von Zahntechnikern attraktiver.
Abschließend möchte ich erwähnen, dass die Digitalisierung es ermöglicht, die Herstellung von Teilprothetik an Unternehmen wie Bego auszulagern, so dass den zahntechnischen Laboren material- und arbeitsintensive oder sicherheitsrelevante Arbeitsschritte erspart bleiben. Wir bei Bego sind mit unserer industriellen Ausrichtung, den Automatisierungen und hohen Arbeitssicherheitsstandards bestens darauf vorbereitet.
Wie stellen Sie sicher, dass die CAD/CAM-Teilprothetik-Versorgungen den hohen Qualitätsstandards und kurzen Lieferzeiten der Dentalbranche entsprechen?
Humez: Ein besonderes Merkmal unserer Produktion ist, mit teilweise erheblichen Mengenschwankungen effizient umgehen zu können. Volumenvariationen und Produktionsspitzen von über 30 Prozent sind nicht ungewöhnlich. Um diese Herausforderungen täglich zu meistern, haben wir Prinzipien etabliert:
Für stabile Prozesse führen wir gründliche Tests durch und validieren unsere Prozesse nach den strengen Normen ISO 13485, bevor wir sie einsetzen. Die Gestaltungsvielfalt der Teilprothetik-Versorgungen wird dabei stets berücksichtigt. Wir gewährleisten über die Wartung und Instandsetzung unserer Maschinen nach einem festen Plan eine maximale Verfügbarkeit.
Wir sind in den Arbeitsabläufen flexibel. Viele unserer Mitarbeiter sind in der Lage, verschiedene Aufgaben zu übernehmen, um auf wechselnde Arbeitsbelastungen reagieren zu können. Wir unterstützen dies mit einem umfangreichen Trainingsprogramm.
Der Komplexität und den kurzen Durchlaufzeiten begegnen wir mit einer präzisen Steuerung des Produktionsflusses. Unsere Führungskräfte nutzen unser ERP-System, unterstützt durch visuelle Hilfsmittel, die den Arbeitsfortschritt in Echtzeit anzeigen. Dieses Visual Management dient auch der Selbstorganisation unserer Mitarbeiter. Zusätzlich wird der Produktionsstatus zweimal täglich besprochen. Wir überprüfen so Qualitäts- und Lieferkennzahlen und legen bei Bedarf Verbesserungen fest.
Unsere Abteilungen für Forschung und Entwicklung sowie Prozessoptimierung widmen sich stetig den Verbesserungen und Innovationen. Dabei setzen sie die Prinzipien der LEAN-Methodik ein. Investitionen in Technologie und die Fortbildung unserer Mitarbeiter gehören wesentlich zu unserer Strategie. Das alles mündet regelmäßig in Optimierungen, die Effizienz und Qualität steigern.
Was sind für Ihre Kunden die Herausforderungen, um die Transition von analoger zu digitaler Fertigung zu schaffen und wie unterstützt Bego hier?
Humez: Unsere Kunden erkennen die Vorteile der Digitalisierung, unser Erfolg in den letzten Jahren ist der beste Beweis dafür. Die Transition bringt allerdings Herausforderungen mit sich. Unsere Kunden müssen sich mit neuen Technologien und Software vertraut machen und auf dem neusten Stand bleiben. Dies erfordert Schulungen und Weiterbildung.
Zahntechniker müssen digitale Workflows integrieren und effizient gestalten. Dabei müssen sie umlernen, beispielsweise das Einhalten von Designvorgaben für Teilprothetik-Versorgungen im 3D-Druckverfahren. Neue Investitionen sind erforderlich, was für kleinere Labore oder Einzelpraxen eine finanzielle Herausforderung darstellen kann.
Bego unterstützt seine Kunden auf vielfältige Weise. Wir übernehmen zum Beispiel das Design von Teilprothetik. Für Kunden, die noch analog arbeiten, erfolgt dies anhand des Gipsmodells, das wir einscannen. Für Kunden, die bereits über Scanner und CAD-Software verfügen, modellieren wir die Versorgungen anhand des von ihnen gesendeten digitalen Abdrucks. Jedes Design wird selbstverständlich vom Kunden freigegeben, bevor wir es in Produktion geben. Kunden, die digital modellieren, begleiten wir zu Beginn, um ihr Feedback zu sammeln und Designempfehlungen zu besprechen. Mit visuellen Hilfsmitteln und Leitfäden erleichtern wir die Kommunikation und fördern das gegenseitige Verständnis.
Ergänzend dazu bietet Bego Seminare an, die in der Nutzung von CAD/CAM-Technologie, speziell für Teilprothetik, schulen. Diese Trainings finden online oder in unserem Trainingszentrum statt.
Welche Entwicklungen erwarten Sie in der Teilprothetik in den nächsten Jahren?
Humez: Wir erkennen weiterhin ein Innovationspotenzial in der CAD/CAM-Technologie für Teilprothetik. Moderne intraorale Scanner ermöglichen es bereits, Abdrücke mit einer solchen Präzision herzustellen, dass sie direkt für das Design und die Produktion von Teilprothetiken geeignet sind. Dies eliminiert die Notwendigkeit für klassische und unangenehme Abformungen bei Patienten. Wir sind überzeugt, dass sich dieser fortschrittliche Ansatz zunehmend durchsetzen wird, Gipsmodelle überflüssig macht und den Arbeitsprozess erheblich vereinfacht und beschleunigt.
Die künstliche Intelligenz verspricht weitere Fortschritte in diesem Bereich. Die Möglichkeiten sind vielfältig: Sie reichen von der Automatisierung des Designprozesses bis hin zur Optimierung von Fertigungsparametern bei der Herstellung von Teilprothetik. KI-gestützte Bildgebung mit Geometrieerkennung könnte beispielsweise die Automatisierung manueller Prozesse ermöglichen.
Neue 3D-Drucktechnologien könnten innovative Produkte hervorbringen. Denkbar wäre beispielsweise die Ergänzung des 3D-gedruckten Metallgerüsts um gedruckte Gingivaanteile und Zähne.
All diese Entwicklungen ermöglichen es, noch proaktiver, patientenspezifischer und präziser zu arbeiten, was die Qualität und Sicherheit für Patienten weiter erhöht. Bego arbeitet bereits an diesen Lösungen. Unser Anspruch ist es, das Bestehende ständig zu hinterfragen und zu verbessern, um Mehrwert für unsere Kunden und deren Patienten zu schaffen.
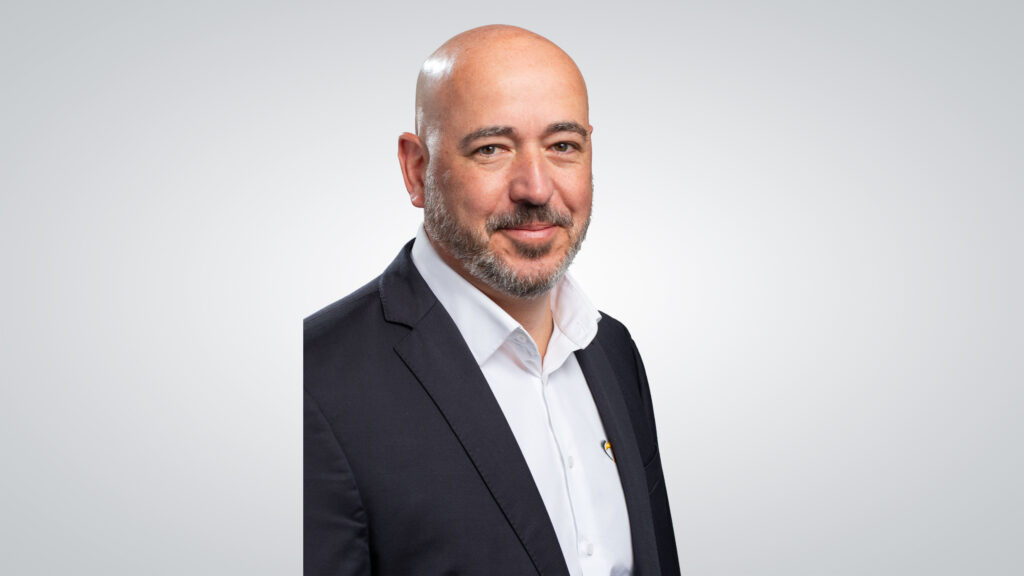
Bego bietet eine Webseminar-Serie zur Hybridfertigung im Labor, die für einen erfolgreichen Einstieg in die Bego-Medical-Hybridtechnik Stück für Stück anleitet.
EMF Legierungen Modellguss
Kontakt
Bego Unternehmensgruppe
Wilhelm-Herbst-Straße 1
28359 Bremen
Tel. +49 421 20280
info@bego.com
www.bego.com
Interview
Weitere Beiträge zum Thema