Interview
Produkte & Lösungen
10.06.24
Polierst Du noch von Hand?
Effizientes Präzisionsfinish mit den Otec Anlagen EF-Smart T und Maxi-Dental
Die Politur von Modellgüssen und Schienen ist ein wichtiger Schritt im Fertigungsprozess. Durch Optimierungen können hier nicht nur Zeit und Ressourcen eingespart, sondern auch die Gesundheit der Mitarbeiter geschont werden. Ztm. Gerd Kock, Ztm. Thorsten Brinkmann und Ztm. Heiko Jeworski vom Labor Kock Dental erzählen, welche konkreten Prozessveränderungen sie in ihrem Dentallabor implementiert haben. Luis Schumacher von der Otec Präzisionsfinish GmbH, die seit mehr als 25 Jahren Anlagen „Made in Germany“ für das Oberflächenfinish entwickelt und produziert, gibt dazu Einblicke in die Poliergeräte Maxi-Dental und EF-Smart T.
Es ist beeindruckend zu sehen, wie sich Dentallabore den Herausforderungen des Fachkräftemangels stellen, indem sie auf Digitalisierung und innovative Technologien setzen. So auch das Labor Kock Dental mit 300 Mitarbeitern an sechs Standorten. Die Fokussierung auf die Digitalisierung von Prozessen ermöglicht es, die wertvolle Expertise der Zahntechniker gezielt dort einzusetzen, wo sie am meisten gebraucht wird – beim individuellen händischen Finishing von Versorgungen. Besonders interessant ist der Ansatz, Prozesse zu optimieren, um Zeit zu sparen und die Effizienz der Zahntechnik zu steigern. Auch bei der Politur von Modellgüssen und Schienen.
Ihr habt für euren Hauptsitz in Wallenhorst die Otec Geräte Maxi-Dental und EF-Smart T angeschafft. Was waren für euch die Beweggründe?
Gerd Kock: Kennengelernt haben wir die Poliergeräte auf der IDS 2023. Die Maxi-Dental wurde von Otec für das maschinelle Polieren von Aufbissschienen und die EF-Smart T für das Polieren von Modellguss vorgestellt. Das fanden wir sehr spannend. Bevor wir neue Technologien und Techniken in unseren Laboren in Richtenberg, Berlin, Pritzwalk und Rostock implementieren, werden sämtliche Innovationen bei uns in Wallenhorst getestet. Direkt auf der IDS haben wir das Maxi-Dental Gerät gekauft und, nachdem wir hier in Wallenhorst von der Polierleistung überzeugt waren, weitere Geräte angeschafft.
Wie viele Geräte sind bei euch mittlerweile im Einsatz?
Gerd Kock: Insgesamt sind es sieben Otec Geräte: zwei Maxi-Dental in Wallenhorst und je ein Gerät in Richtenberg und Berlin. Eine EF-Smart T haben wir in Wallenhorst integriert sowie je ein Gerät in Richtenberg und Berlin.
Was sind die Haupteinsatzgebiete der
Maxi-Dental und EF-Smart T?
Heiko Jeworski: In der Maxi-Dental polieren wir ausschließlich Schienen: Aufbissschienen, harte, weiche, hart-weiche und thermoplastische Schienen. 3D-gedruckte Schienen befinden sich bei uns gerade in der Testphase mit den Materialien Keysplint Soft als flexibles Material mit Memory Effekt bei Mundtemperatur und Keystone. Im Fräsprozess nesten wir maximal anderthalb Schienen pro Rohling, beim Asiga-Drucker passen etwa 15 Schienen auf eine Bauplattform. Hier sehen wir eine sehr lukrative Möglichkeit für unsere Labore. Der 3D-Druckprozess ist top und mit dem Maxi-Dental Gerät haben wir einen abgerundeten Workflow.
Thorsten Brinkmann: Mit der EF-Smart T polieren wir Modellgüsse mit unterschiedlicher Anzahl von Klammern.
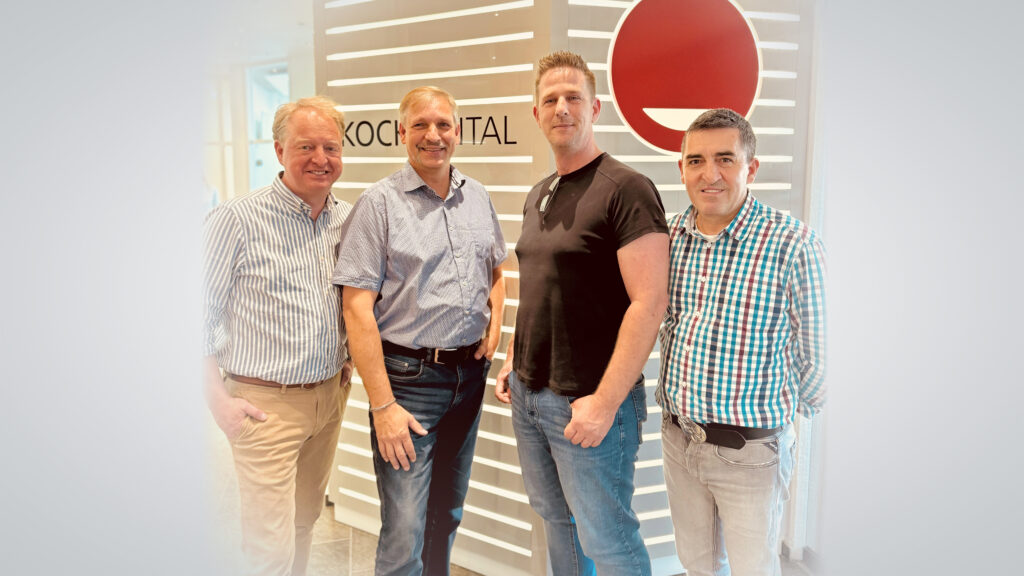
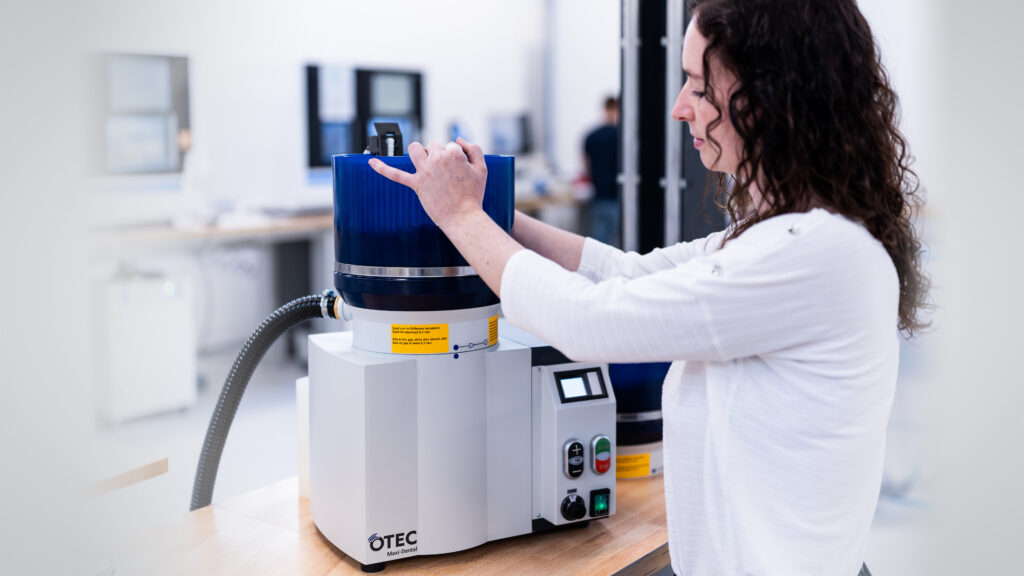
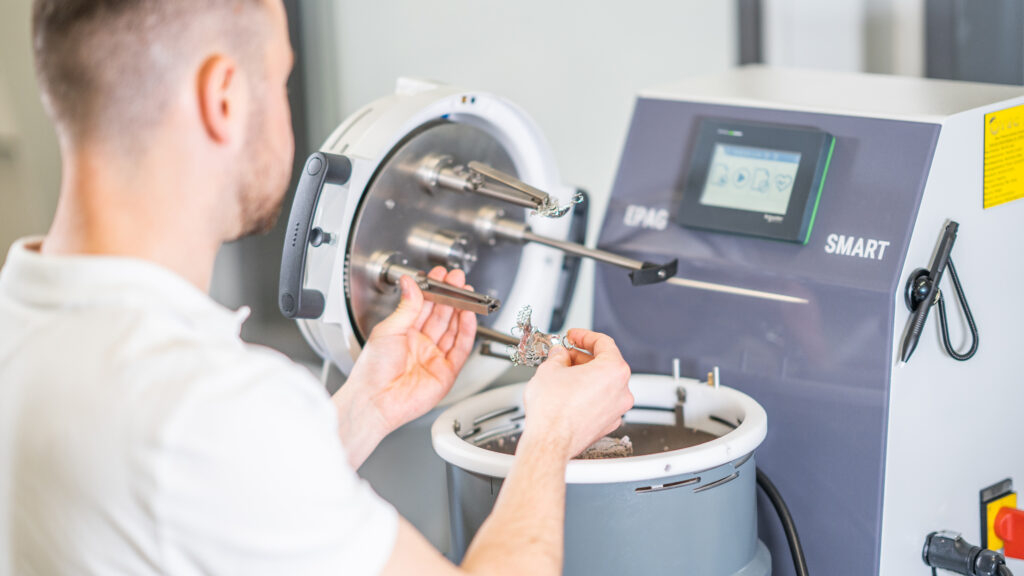
Wie sieht es mit den Prozesszeiten aus und wie viele Schienen respektive Modellgüsse werden poliert?
Heiko Jeworski: Die Prozesszeiten bei den Schienen betragen zweimal 45 Minuten für Vorschleifen, Feinschleifen und Polieren. Das Schleifen erfolgt mit einem Abrasivkörper aus Aluminiumoxid und das Polieren dann mit Polierkörpern aus Zirkonoxid mit Körnern und Stiften zu je 50 Prozent bei 240 Umdrehungen/Minute. Bearbeitet werden zeitgleich bis zu zehn Schienen. Die Geräte sind dreimal täglich im Einsatz, also polieren wir automatisiert circa 30 Schienen am Tag, ohne manuelle Nacharbeit. In Wallenhorst produzieren wir Schienen mit steigender Tendenz, vor allem auch, weil Schienen eine Kassenleistung darstellen, also ein in sich stimmiger, zu 95 Prozent automatisierter Prozess mit hoher Wertschöpfung sind.
Thorsten Brinkmann: In der EF-Smart T werden drei Modellgüsse in 15 bis 20 Minuten poliert. Vorher werden sie noch von Hand gummiert. Ohne Gummierung ist aus unserer Sicht die Oberfläche nicht glatt genug. Ein Gummiervorgang dauert fünf bis zehn Minuten als Vorbereitung bei einer CoCr-Versorgung mit ein bis zwei Klammern. Die Bestückung und der Start des Gerätes mit drei Indikationen erfolgt in einer Minute. Dann wird der Deckel geschlossen, das Programm ausgewählt und los geht’s mit dem Polieren. Sämtliche Klammern werden in der EF-Smart T auch von innen auspoliert, dabei wird kaum etwas abgetragen. Die Form der Werkstücke bleibt unverändert. Wir sparen das manuelle Polieren des Modellgusses. Pro Klammer ist das eine Zeitersparnis von circa fünf Minuten. Und vor allem muss man händisch sehr gut polieren mit viel Bewegung, damit der Glanz gleichmäßig ohne Striemen drauf ist. Wenn einer nur in eine Richtung poliert, hat er überall Striemen auf der Versorgung. Das macht die EF-Smart T natürlich nicht, hier ist alles gleichmäßig und vor allem bei konstant hoher Qualität.
Welches Material wird bei der EF-Smart T genutzt?
Thorsten Brinkmann: Wir verarbeiten ein fertiges Granulatgemisch, das in Beuteln im richtigen Mischverhältnis geliefert wird. Das Material ist geruchsarm, muss nicht mehr geschüttelt werden und kann länger verarbeitet werden.
Luis Schumacher: Seit wir bei der IDS 2021 auf den Markt gekommen sind, haben wir eine disruptive Entwicklung erlebt. So haben wir seitdem neue Halter für Kronen und Brücken, Modellguss, KFO-Teile und auch Stege entwickelt. Abgesehen von der Prozessentwicklung, bei der wir es geschafft haben, unser Verfahrensmittel gebrauchsfertig für den Kunden zu versenden. Dies hat den Vorteil, dass zum einen der Kunde nicht mehr selbst mischen muss, auf der anderen Seite aber auch nichts „falsch“ machen kann. Es hat ehrlich gesagt auch seine Zeit gebraucht, bis wir den Dentalkunden kennengelernt und verstanden haben. Wir wollen stabile Prozesse und zufriedene Kunden. Eine weitere Verbesserung ist die Referenzelektrode. Damit wird die Leitfähigkeit des Gemischs ermittelt und kann durch die Zugabe von destilliertem Wasser verbessert werden.
Welche spezifischen Vorteile bietet die EF-Smart T in Bezug auf die Präzisionsbearbeitung beziehungsweise manuelle Ausarbeitung von Nichtedelmetall-Werkstücken?
Thorsten Brinkmann: Mit der circa fünfminütigen Vorgummierung haben wir den Vorteil, dass der Polierprozess maximal 20 Minuten dauert. Damit gewährleisten wir einen gleichmäßigen Hochglanz, auch in den Ecken und an Stellen, die normalerweise schwer zu erreichen sind, wie zum Beispiel bei einer Klammer, wo man nicht so nah herankommt. Die Oberflächen werden sanft und homogen umströmt, wodurch sogar in schwer zugänglichen Bereichen und den Innenseiten der Klammern tolle Glättungs- und Politureffekte erzielt werden. Die manuelle Politur und das Glanzbad wurden durch das Electro-Finish-Verfahren ersetzt. Manuell musste man 20 Minuten in Hochglanz polieren, die Zeiteffizienz ist immens. Eine gewisse Ungenauigkeit gab es beim manuellen Polieren immer und die Mitarbeiter lieben es, das nicht mehr machen zu müssen. Und vor allem muss man sich nicht mehr die Finger heiß polieren und die Finger bleiben sauber.
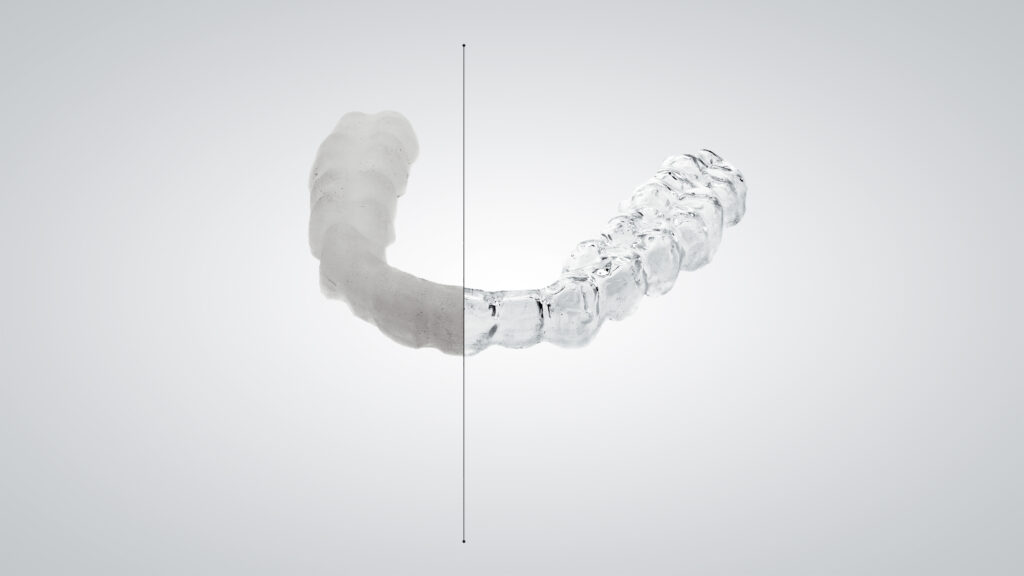
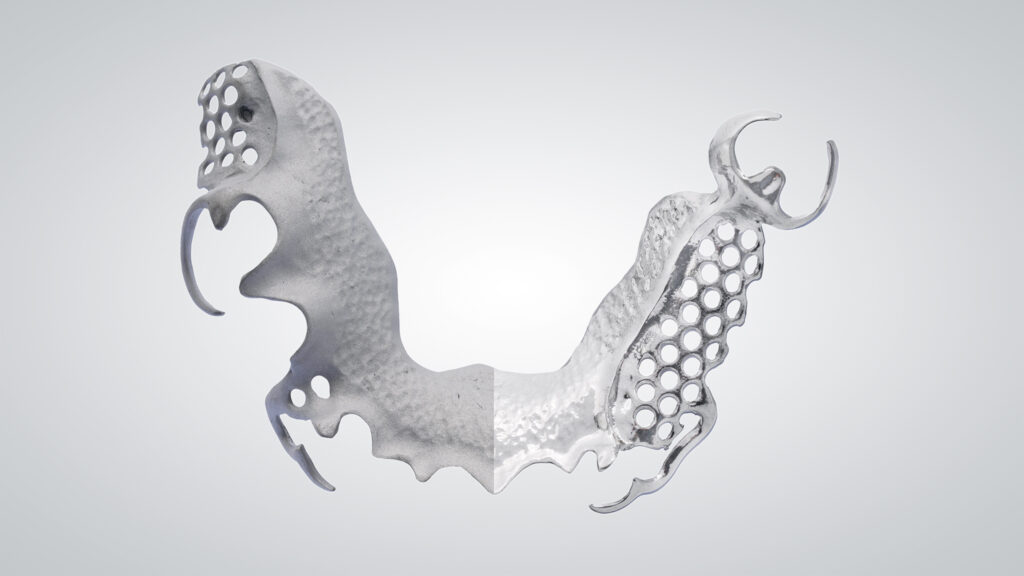
Bevor ihr mit dem Maxi-Dental Gerät gearbeitet habt, wie sah euer Workflow da aus?
Heiko Jeworski: Früher haben die Mitarbeiter die Schienen per Hand poliert und das dauerte wesentlich länger. Mit der Maxi-Dental sind die Schienen jetzt gleichmäßig an allen Stellen poliert.
Was sind die „Painpoints“, die durch die Bearbeitung mit den Maxi-Dental Geräten gelöst wurden? Und wie sieht der Return on Investment (ROI) seit Einführung der Geräte bei euch aus?
Heiko Jeworski: Vor allem haben wir viel Stress aus der Arbeitssituation genommen und die Überlastung der Mitarbeiter durch die Geräte ausgeglichen. Die beiden Geräte ersetzen hier in Wallenhorst eine komplette zahntechnische Fachkraft. Wir arbeiten damit dem Fachkräftemangel entgegen. Die Geräte unterstützen uns im Tagesablauf sehr, um die bestehende und Mehrarbeit mit weniger Mitarbeitern zu stemmen. Die Anschaffungskosten sind überschaubar, die Prozesskosten betragen laut Hersteller circa 0,50 Euro pro Schiene, also zusammengefasst sind die Kosten schnell amortisiert. Und wir sind echt begeistert, weil die Mitarbeiter jetzt viel mehr Luft und Zeit für das ästhetische Finish haben. Die Mitarbeiter lieben die Geräte.
Welche Voraussetzungen mussten geschaffen werden, um die Geräte in bestehende Arbeitsabläufe in euren Dentallaboren zu integrieren?
Heiko Jeworski: Wenig, etwas Platz für die Tischmaschine, Plug-and-Play-Funktion und eine kurze Schulung, fertig! Wir haben die Geräte bei der Flussfisch GmbH gekauft. Die Schulung, die Beratung und der Support sind super. Intern führe ich die Schulungen bei den Mitarbeitern durch. Die Verantwortung für die Geräte wurde an eine Kollegin übertragen, die die Vorbereitung der Geräte für den täglichen Gebrauch übernimmt. Dazu gehört Wasser einfüllen, säubern und Granulat einfüllen. Im Sommer wird das Wasser zweimal pro Woche und in den Wintermonaten wöchentlich gewechselt. Also ein gänzlich einfacher Ablauf. Zwischendurch haben wir direkt Kontakt zu Otec, damit sich keine Fehler einschleichen und wir von den Neuerungen seitens des Herstellers profitieren.
Thorsten Brinkmann: Für die EF-Smart T brauchten wir nicht viel vorzubereiten. Der Platz wurde ausgesucht und das Gerät aufgestellt. Es kann mit 230 V betrieben werden, ohne Druckluft und ohne zusätzlichem Wasserbedarf. Klar, das Gerät muss immer kontrolliert werden. Sauberes Arbeiten ist wichtig, einmal pro Woche schauen wir nach der Flüssigkeit und füllen bei Bedarf nach.
Bitte gebt mir eine Rückmeldung zu der Oberflächengüte bei Aufbissschienen.
Heiko Jeworski: Die Oberflächengüte ist sehr schön, wir sind total begeistert davon. Durch den zweistufigen Prozess werden Strukturen wie Fräsrillen in der Oberfläche restlos entfernt und Kanten verrundet. Die Kunden sind zufrieden, es gibt nur positive Rückmeldungen!
Wie zuverlässig und prozesssicher arbeiten die Otec Geräte?
Thorsten Brinkmann und Heiko Jeworski: Die Geräte arbeiten sehr zuverlässig und durchgängig, absolut top ohne Ausfälle.
Kontakt
Dental Labor Kock Betriebs GmbH & Co. KG
Hansa Str. 85
49134 Wallenhorst
Tel. +49 5407 83820
info@kock.dental
www.kock.net
Otec Präzisionsfinish GmbH
Heinrich-Hertz-Str. 24
75334 Straubenhardt
Tel. +49 7082 491120
info@otec.de
www.otec.de
Interview
Weitere Beiträge zum Thema